Wear and tear are lingering threats to industrial work, adding to costs, prolonging time, and compromising the overall effectiveness of the operations. Ceramic materials are a way to go, curtailing these issues. Silicon Carbide (SiC) and Tungsten Carbide (WC) are two commonly available options. We at Gorgeous Ceramics, in this article will compare both the materials and their effectiveness in wear applications.
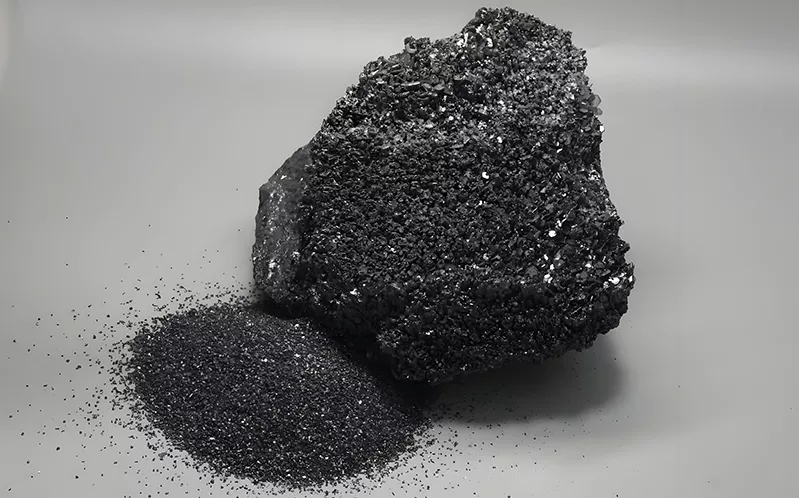
Silicon Carbide
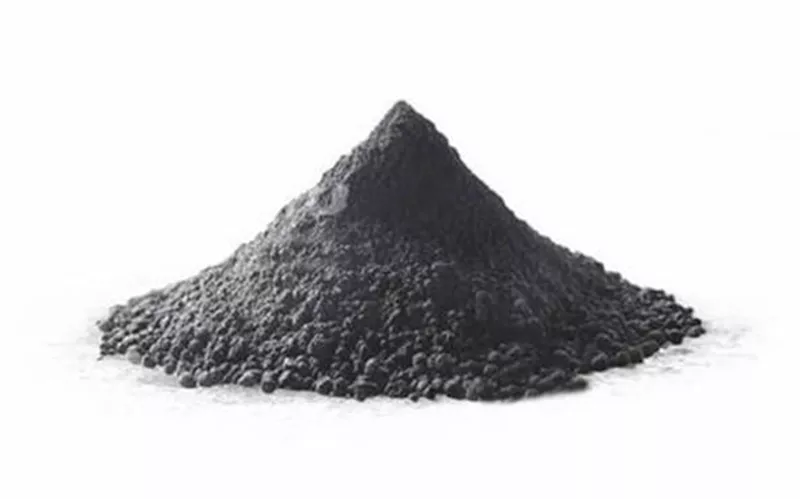
Tungsten Carbide
What is Silicon Carbide
Silicon Carbide is well-known for its suitability in chemical and temperature-sensitive applications. This material is an amalgamate of carbon and Silicon elements, with their atoms making covalent bonds and giving the material a crystalline structure.
After the diamond, this is the hardest element. This makes it suitable for a long list of applications involving wear. Due to Silicon Carbide’s non-oxide properties, it is corrosion free, further adding up in its reliability.
What is Tungsten Carbide
Tungsten Carbide WC, as its name indicates, is the product of Tungsten and carbon manufactured through a process called Sintering. WC has a long history of use in industrial applications. These materials are good to go, whether it’s about wear, abrasion, heat, or chemical resistance.
Silicon Carbide Vs. Tungsten Carbide in Wear Applications
Cost is a vital, but not the only factor impacting the choice of wear material. In the long run, understanding a material’s reliability under different working situations like extreme pressure, temperature, abrasion, and exposure to chemicals is critical to understanding its overall efficiency.
Tungsten Carbides, for example, have high prices, which is justified by their high compressive strength of up to 6833Mpa. However, in operations involving extreme temperatures, plastic deformation renders much of this strength futile. This eventually makes them not a very suitable option for high-stress applications. On the other side, material with high-temperature resistance can prove to be a better alternative.
In this backdrop, Silicon Carbide (SiC) is a way to go. It is most often applied in operations where high temperature and chemical resistance is required. However, both the ceramics require careful consideration of a multitude of factors when choosing when choosing between them. These factors are discussed below.
Abrasive Conditions
The hardness of ceramics is a primary aspect of wear applications. The harder the ceramic, the less prone it will be to damage. On the Mohs scale, Silicon Carbide’s hardness level is 9.5, outpacing Tungsten’s 8.5-9. Thus, Silicon Carbide is more recommended in abrasive-sensitive applications.
In terms of density, SiC is at the bottom end with 3.21g /cm³, much lower than Tungesten’s 15.6g/cm³. This low density makes Silicon Carbide easy to handle. Additionally, its high scratch resistance further makes it a win-win situation.
Heavy Slurry and Extreme Pumping Conditions
Slurry and pumping machines must be compatible to work effectively in abrasive and corrosion environments. Silicon Carbide is considered best to work in these conditions. Its low friction coefficient ensures minimum wear and energy loss.
Conversely, Tungsten Carbide, due to its cobalt bonding, is highly vulnerable to strong acids. However, this can be managed through extra chromium and molybdenum coatings, but this will result in high final costs. Thus, Silicon Carbide is a preferred choice for such applications.
High-Pressure Environments
Drilling applications such as oil and gas involve high pressures, and their respective seals should be strong enough to endure these pressures. Tungsten Carbides have a good combination of high density and strength, so its a perfect fit in such cases. However, if we consider strength only, Silicon Carbides are also useful but are outperformed by Tungsten due to their high density.
Rapid Temperature Changes
Machines used in high-temperature applications such as furnaces must be made with temperature-resilient materials. Thus, temperature resilience must be taken into consideration while choosing between Silicon and Tungsten Carbide.
Silicon Carbide’s temperature expansion coefficient is around 4 to 4.5×10⁻⁶/°C, as compared to Tungsten’s 5.00 to 6.00 10⁻⁶/°C, which is low and considered most suitable. But that’s not all. Regarding thermal conductivity, Silicon also excels in that parameter, with conductivity ranging between 120 and 170 W/mK compared to Tungsten’s 84 to 100W/mK.
Differences in Durability and Wear Resistance
Silicon Carbide excels in strength and temperature resistance. In applications where the probability of wear and friction is high, SiC can be a reliable choice. Its non-oxide nature, coupled with its low-temperature coefficient, prevents deformation and ensures its durability in a diverse range of applications.
On the other hand, Tungsten’s rigidity and strength are unmatchable. This makes the ceramic durable during high-pressure applications for extended periods of time. So for applications not vulnerable to temperature and chemical exposure, Tungsten Carbide can be a go-to solution.
How to Choose Between Silicon Carbide and Tungsten Carbide Mechanical Seals
When choosing between Silicon or Tungsten Carbide, it is important to understand their use case first. This includes careful consideration of multiple aspects like the presence of fluids, temperature ranges, changes in pressure levels, abrasion, and chances of corrosion.
Tungsten’s high density, combined with its sheer strength, makes it extensively compatible in high-pressure applications. Contrary to that, Silicon Carbide only lags behind in density and comes with greater strength, temperature handling, corrosion, and abrasion resistance. Silicon Carbides also remain very much stable when exposed to other chemicals.
Depending on the above analysis, it is safe to say that Silicon Carbides are well-suited for all types of wear applications except those involving extreme pressure. Further, its price point, which is low compared to Tungsten, makes it more favorable, but the ultimate choice depends on each process’s preferences.
The Bottom Line
Both Silicon Carbide and Tungsten Carbide offer unique advantages and limitations. While Tungsten Carbide remains a popular choice for industrial applications, Silicon Carbide emerges as a cost-effective and versatile alternative. Gorgeous Ceramics is dedicated to providing innovative solutions tailored to your needs. Contact us today to discuss your project and discover how our expertise can elevate your processes.