Committed to providing you with special size and shape customization and solving batch color difference ceramic arm provider!
Ceramic Arm/Ceramic End Effector Supplier
Customize Your Ceramics
Ceramic Arm Description
Ceramic robotic arms, also known as ceramic robotic fingers, wafer trays, round wafer robotic arms, etc., are mainly used for the transportation and handling of semiconductor equipment, and are responsible for delivering wafer silicon wafers to designated locations.
GORGEOUS product features:
▫️High product precision
▫️Excellent air tightness
▫️Good high temperature resistance
▫️Controllable surface resistivity
▫️Strong acid and alkali resistance and corrosion resistance, adaptable to various extreme harsh environments
🔷Self-tightness test: turn off the vacuum air source, negative pressure –85Kpa to -80Kpa, for more than 60s
🔷Wafer adsorption test: turn off the vacuum air source, negative pressure -80Kpa to -25Kpa, for more than 35s
Guarantee Manufacturing & Shipping Time
GORGEOUS is a leading manufacturer of ceramics for semiconductor wafer processing. We have 15 years of technology and experience in manufacturing advanced ceramics, and we are constantly optimizing and upgrading the manufacturing process of semiconductor ceramics. We can customize various components for you, such as ceramic arms, robot end effectors, ceramic wafer chucks, etc.
The packaging of the ceramic arm can be based on your needs, using hard environmentally friendly materials or soft foam protection.
Our ceramics are shipped all over the world, and the transportation of ceramics is affected by your location. We will quickly manufacture for you according to your plan and choose the best transportation method. The fastest air freight in North America, arrives in 7 days.
GORGEOUS chooses to cooperate with several leading logistics companies, including:
- MSC (Mediterranean Shipping Company)
- Maersk
- CMA CGM
- COSCO
- Hapag-Lloyd
- DHL
- UPS
- FedEx
- TNT
We work with multiple freight forwarders to guarantee you efficient shipping options at lower prices, on-time delivery, and no hidden fees!
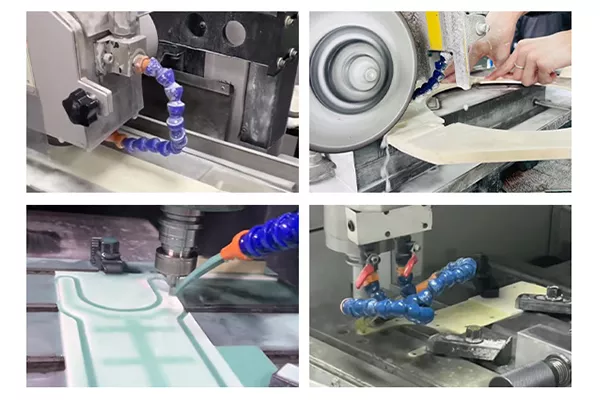
Manufacturing
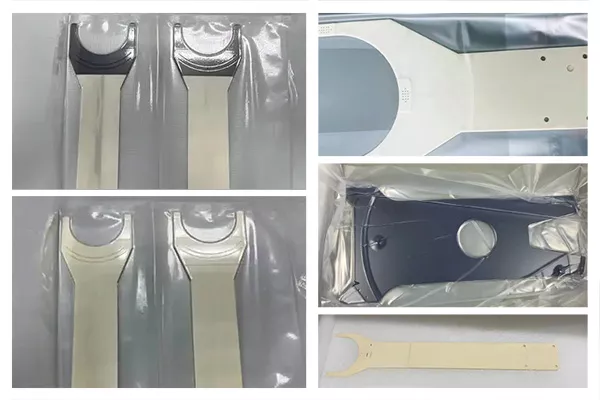
Packing
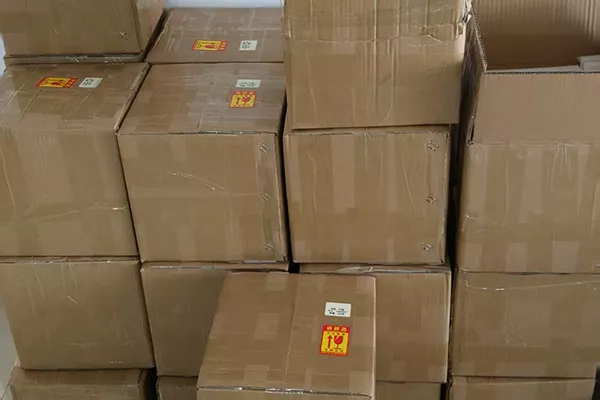
Loading
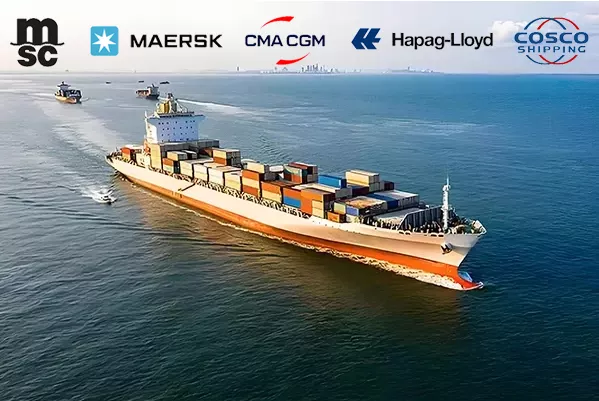
Transportation
Main Performance of Ceramic Arm/Ceramic End Effector
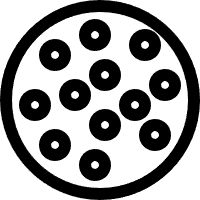
Lightweight
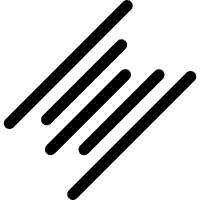
Wear-Resistant
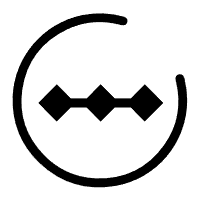
Corrosion Resistant
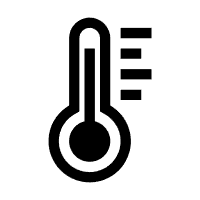
High Temperature Resistance
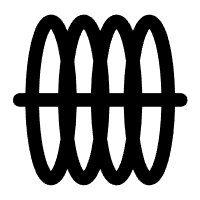
Strong Insulation
GORGEOUS Customizable Product Accuracy Reference
Minimum | Maximum | |
Overall Thickness | 1.5mm | 4mm |
Cavity Thickness | 0.5mm | 0.7mm |
Thickness of The Gap Between The Cavity and The Surface | 0.5mm | – |
Width of Cavity | 2mm | 6mm |
Distance Limit From Edge | 2mm | – |
Adsorption Pore Size | 0.5mm | – |
Void Length | – | 360mm |
*The specific accuracy needs to be determined according to the actual product material, shape and process requirements.
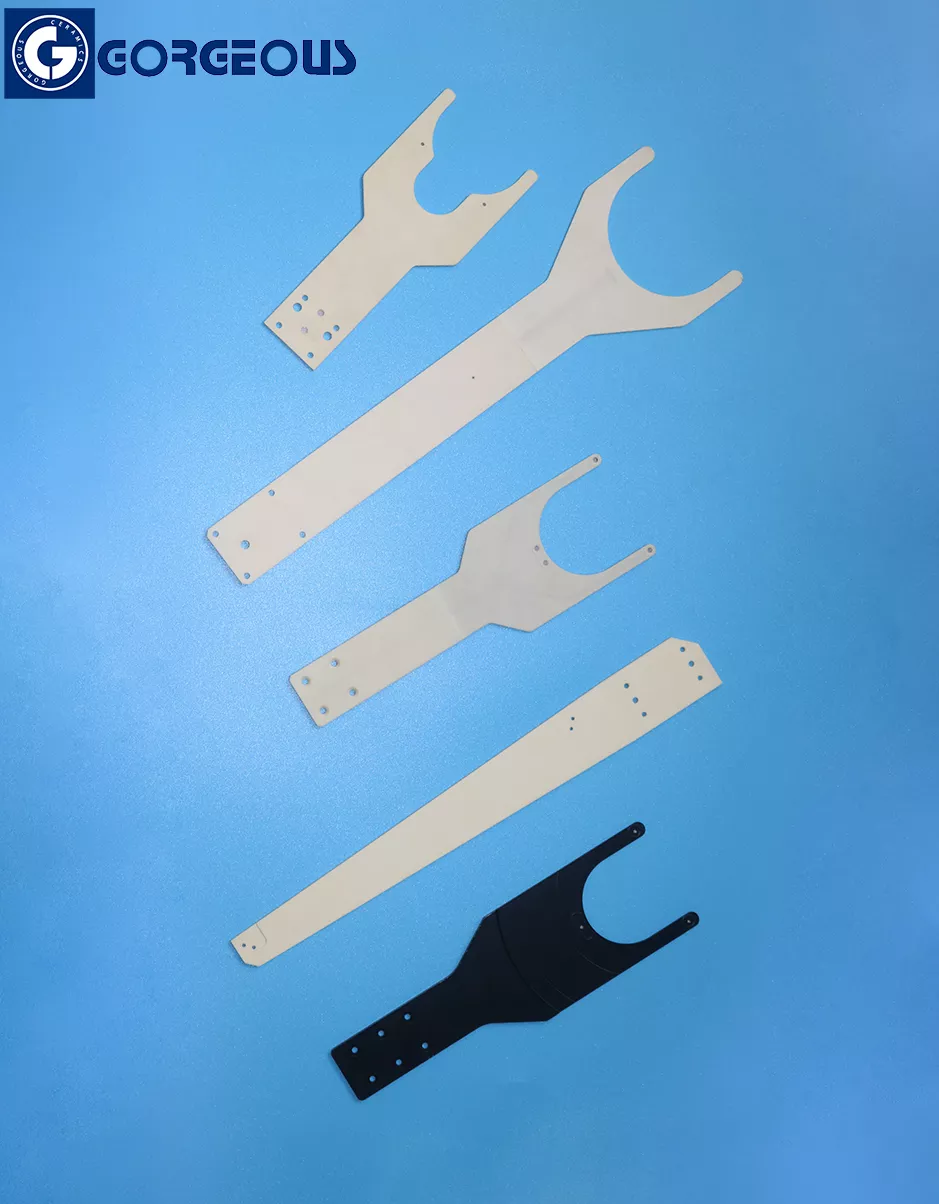
Customize Various Types of Semiconductor Ceramic Arm
Customized Arm Material Parameters and Selection
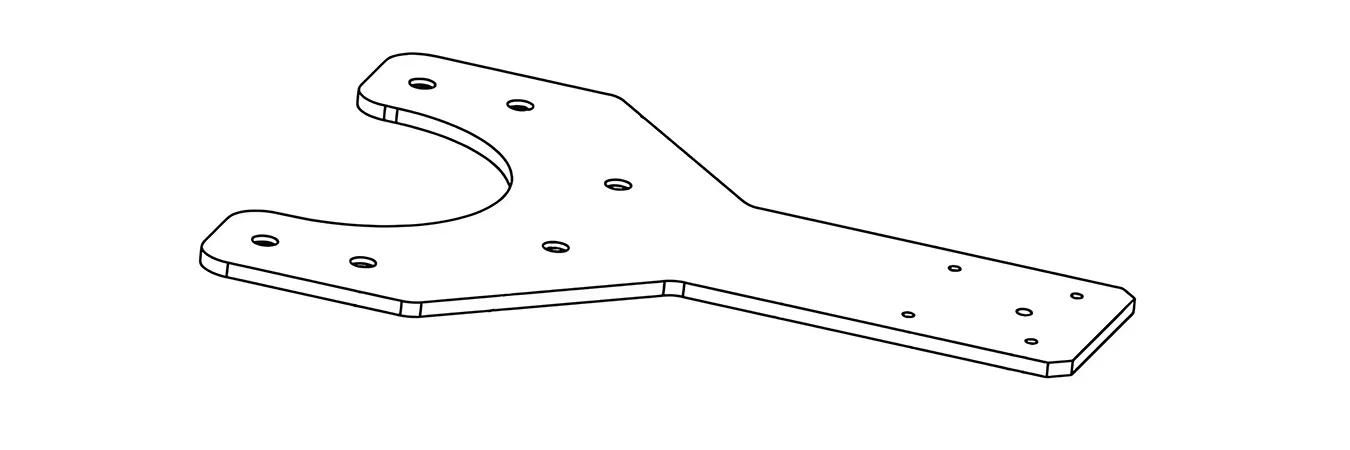
Item | Unit | Zirconia |
Density | g/cm3 | 6.0 |
Zirconia Content | % | 94.4% |
Grain Size | µm | 0.5 |
Rockwell Hardness(45N) | R45N | 78 |
Vickers Hardness(Load 500g) | GPa(Kg/mm2 ) | 11.5(1175) |
Flexural Strength (20℃) | MPa | 800 |
Compressive Strength (20℃) | MPa | 2000 |
Fracture Toughness(20℃) | MPam1/2 | 9.0 |
Thermal Conductivity(20℃-400℃) | W /(m.k) | 2.5 |
Coefficient of Thermal Expansion | 10-6 /℃ | 9.6 |
Thermal Shock Resistance | △T℃ | 250 |
Property | Unit | AL2O3 99.7 | AL2O3 99.5 | AL2O3 99 | AL2O3 95 |
Purity | — | 99.7% | 99.5% | 99% | 95% |
Density | g/cm3 | 3.92 | 3.9 | 3.8 | 3.7 |
Bending Strength | MPa | 375 | 370 | 340 | 304 |
Compressive Strength | MPa | 2450 | 2300 | 2250 | 1910 |
Elastic Modulus | GPa | 380 | 370 | 330 | 330 |
Fracture Toughness | MPam1/2 | 4.5 | 4.3 | 4.2 | 3.8 |
Hardness | HRA | 91 | 91 | 90 | 89 |
Vickers Hardness | HV1 | 1600 | 1550 | 1450 | 1400 |
Thermal Expansion Coefficient | 10- 6 K-1 | 7.8 | 7.8 | 7.7 | 7.5 |
Thermal Conductivity | W/mk | 32 | 32 | 25 | 25 |
Thermal Shock Stability | △T.℃ | 220 | 220 | 200 | 200 |
Maximum Operating Temperature | ℃ | 1750 | 1750 | 1700 | 1500 |
Volume resistance at 20℃ | Ω·cm | 1015 | 1015 | 1014 | 1014 |
Dielectric Strength | KV/mm | 22 | 20 | 16 | 15 |
Dielectric Constant (room temperature) | / | 10 | 11 | 11.5 | 11 |
MHz Dielectric Loss Factor | tan δ | 1×10-3 | 1×10-3 | 3×10-3 | 3×10-3 |
Item | Unit | Silicon Nitride |
Density | g/cm3 | >3.2 |
Hardness | – | HRA90 |
Vickers Hardness(Hv50) | HV0.5 | >1550 |
Modulus of Elasticity | GPa | 290 |
Flexural Strength | MPa | >600 |
Compressive Strength | MPa | 2500 |
Fracture Toughness | MPam1/2 | >6.0 |
Maximum Use Temperature | ℃ | 1200 |
Thermal Conductivity | W /(M·K) | 15-20 |
Thermal Expansion Coefficient | 10-6/℃ | >3.1 |
Thermal Shock Resistance | △T℃ | 500 |
Specific Heat Capacity | KJ/kg·K | 700 |
Dielectric Strength | KV/mm | 1 |
Dielectric Constant | εr | – |
Volume Resistivity at 20℃ | Ω.cm | 1.0×1012 |
Ceramic Arm/End Effector Standard Size Reference
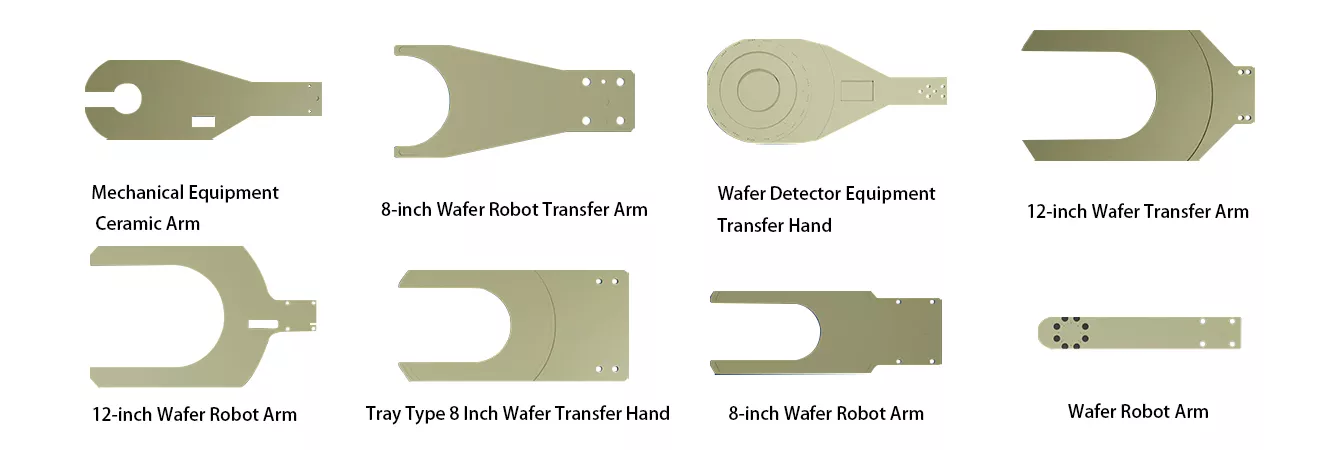
Ceramic arms/end effectors are key components used to handle wafers in semiconductor manufacturing. We can customize them according to the size of the wafer, the type of equipment, and the process requirements. Here are some common standard sizes of ceramic arms for your reference!
Choose the Length of The Ceramic Arm According to The Wafer:
❇️6-inch wafer (150mm): Arm length: about 200-250mm
❇️8-inch wafer (200mm): Arm length: about 250-300mm
❇️12-inch wafer (300mm): Arm length: about 350-400mm
❇️18-inch wafer (450mm): Arm length: about 500-550mm
Ceramic Arm Width and Thickness
❇️Width: Typically 20-50mm, depending on your wafer size and required arm load capacity.
❇️Thickness: Typically 5-15mm, to ensure adequate strength and rigidity and reduce weight.
Arm End Design
❇️Fork design: commonly used for handling wafers, the width and spacing of the forks match the slots of the wafer box
❇️Vacuum suction cup design: can directly absorb the wafer, the common suction cup size is 10-20mm
❇️Edge clamping design: used for special processes, the clamping area width is 5-10mm
What Are The Uses of Ceramic Arms?
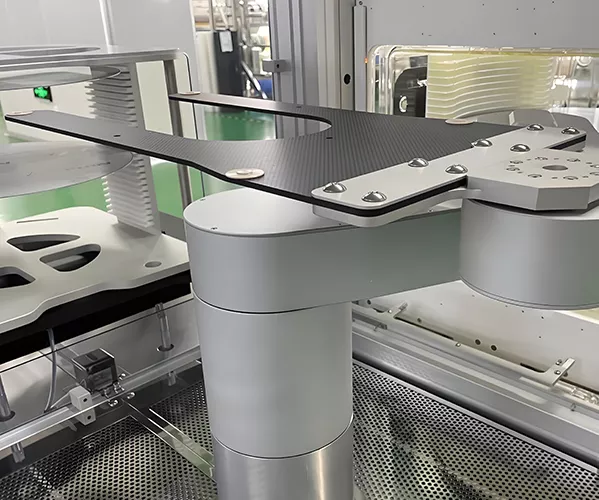
Industrial Robot Arm
Ceramic arms are used in high-precision, wear-resistant and corrosion-resistant industrial robots, and can work stably in some precision processing and high-temperature environments.
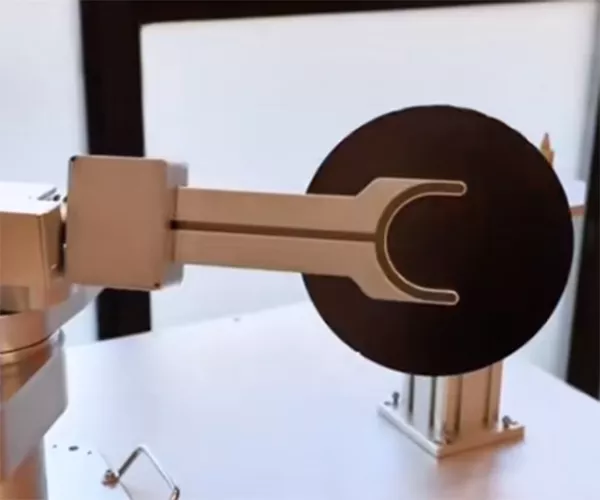
Semiconductor Manufacturing
In the chip manufacturing process, silicon wafers need to be transferred between different process steps (such as lithography, etching, deposition, etc.), and ceramic arms can act as handling manipulators in a dust-free environment.
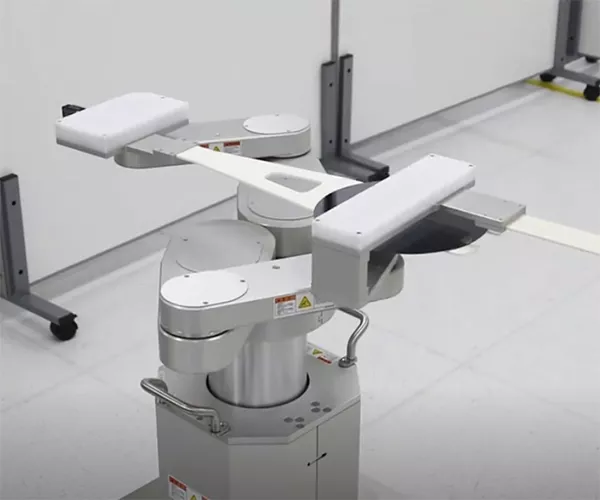
Electronics Manufacturing
Electronic manufacturing ceramic arms are suitable for processes with high cleanliness requirements such as vacuum coating, chip manufacturing, and OLED display manufacturing. They can avoid the influence of thermal expansion of metal materials and improve stability.
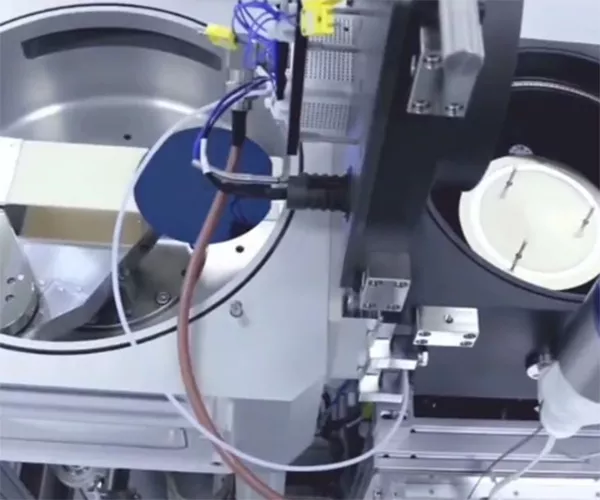
Scientific Research
In laboratory equipment that requires resistance to corrosion and high temperature environments, ceramic arms can be used in fields such as chemical synthesis, plasma experiments and superconductivity research.
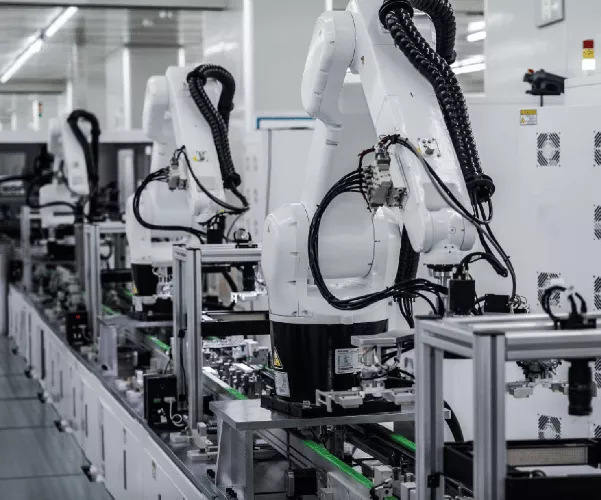
Food and Pharmaceutical Industry
Ceramic materials do not contain metal ion precipitation and are suitable for fields such as food processing and pharmaceutical packaging that require extremely high material cleanliness.
One-stop Ceramic Arm manufacturing service
15+ Years of Experience. High Precision and OEM Design. Professional R&D Team. Competitive Price.
Will the ceramic arm/ceramic end effector wear out over time?
Yes, the ceramic arm will wear out over time, especially in harsh and rough environments. But don’t worry too much, ceramic is a very hard and durable material, as long as it is properly maintained, you can use it for many years.
What would cause a ceramic arm to break?
Rapid temperature changes can cause thermal shock and cause the ceramic arm to break. Overloading, collision or severe impact beyond the rated capacity can also cause rupture.
How often should you check your ceramic arm?
Frequent inspections every week will allow you to detect problems early. Ceramic arms may wear, crack or become loose after long-term use. We recommend that you perform regular maintenance.