International Leading Silicon Carbide Ceramic Solution Provider
15+ years of SSIC and SISI product sales and production experience, customizing silicon carbide ceramic structural parts in various fields for you
Silicon Carbide Ceramics/SIC Ceramic
Customize Your Ceramics
Silicon Carbide Ceramics: High-End Material Solutions Tailored for Your Field
At GORGEOUS, we engineer high-performance silicon carbide (SiC) ceramics for industries where standard materials fall short. Whether your needs require extreme heat resistance, wear resistance, or chemical stability, our custom silicon carbide solutions are engineered to perform reliably in the most demanding environments.
⬜️ Thermal & High-Temp Applications
➡️ Crucibles, Kiln Furniture, Thermocouple Protection Tubes
⬜️ Mechanical & Wear Resistance
➡️ Seals, Wear-resistant Parts, Ceramic Arm
⬜️ Precision Fluid & Gas Control
➡️ Flame Spray Nozzles, Cold Air Ducts
⬜️ Advanced Technology Sectors
➡️ Semiconductor Components, Bullet-Proof Armor
Tell us your requirements - we will provide a custom solution of SiC components for your application. [Contact us] for a free technical consultation.
R&D to Customize Your Silicon Carbide Ceramic Application
◽️Materials Research
GORGEOUS will conduct in-depth research on high-tech materials according to market demand and your specific requirements for product performance, comprehensively consider key factors such as material purity, mechanical properties, electrical properties, thermal properties, high temperature resistance, corrosion resistance, and impact resistance, and select the best material system and additive system. We use formulation design methods such as Taguchi design, DOE single factor or multi-factor multi-level analysis to optimize the material ratio, and prepare samples in combination with corresponding molding and sintering processes, and perform polishing, corrosion and other treatments. Finally, we conduct a comprehensive evaluation based on the process parameters, organizational structure, and performance of the material formula to ensure that your products meet the expected requirements and deliver the best silicon carbide ceramics to you.
◽️Engineering Design
After receiving your requirements, GORGEOUS will guide you to connect the product and engineering design with our professional engineering design engineers and product engineers. After in-depth discussions, we will conduct a full set of engineering product design based on your needs and application scenarios and the company’s technical characteristics.
◽️Process Optimization
We always put product quality, yield, delivery time and customer satisfaction first. Our process engineers and senior managers will always put forward the needs of technology and process optimization and iteration, and hand it over to the R&D department to initiate process optimization projects, optimize the corresponding processes, and always provide you with better quality products.
◽️Mold Design
GORGEOUS’s design engineering team is experienced and familiar with the molding, sintering and processing characteristics of various material systems and products. They can accurately select suitable mold materials and use CAD, SolidWorks, UG and other design software to design matching molds. You can choose different types of molds such as processing molds, 3D printing molds, casting molds, lost foam or lightweight molds according to your needs to support production. At the same time, we can provide product solutions suitable for large, thick-walled, extra-long, extra-thick or complex inner cavity structures.
Features of GORGEOUS Silicon Carbide Ceramic Products
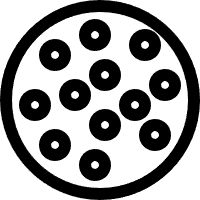
High Purity
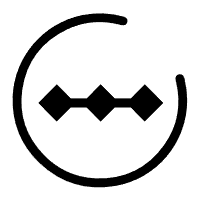
Chemical Stability
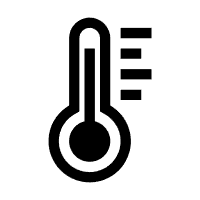
High Temperature Resistance
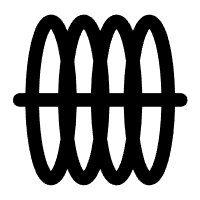
Antioxidant
GORGEOUS Can Provide You with Silicon Carbide Materials
⬜️Pressureless Sintered Silicon Carbide
- Particle size can reach 0.5-1.0μm.
- Ultra-high hardness, excellent wear resistance, Vickers hardness exceeds 2000GPa.
- Excellent bending strength, three-point bending strength greater than 350MPa.
- High temperature resistance up to 1500℃.
- High thermal conductivity and low thermal expansion coefficient (room temperature thermal conductivity>120W/m·K, room temperature CTE<2.5ppm/℃).
- Comprehensive chemical corrosion resistance.
- Can customize large-size and various complex structure ceramic parts for you.
⬜️Reaction-Sintered Silicon Carbide
- Excellent bending strength (>280MPa, 3 times that of quartz material)
- Maximum operating temperature can reach 1350℃
- Chemically stable, resistant to acid and alkali corrosion, low etching rate of acid and alkali washing
- Low thermal expansion coefficient, similar to that of materials such as silicon nitride
- Excellent wear resistance and hardness (>2500GPa)
- Excellent thermal conductivity (room temperature thermal conductivity>160W/m·K)
⬜️3D printing Silicon Carbide
- Particle size is usually 50-100μm
- Excellent wear resistance (Vickers hardness > 20GPa)
- High temperature resistance, can withstand 1300℃
- High thermal conductivity, low thermal expansion coefficient (room temperature thermal conductivity > 100W/m·K, room temperature CTE < 4*10-6 /K)
- Purity can reach up to 99.98%
- Can manufacture large-sized and various complex structural parts for you
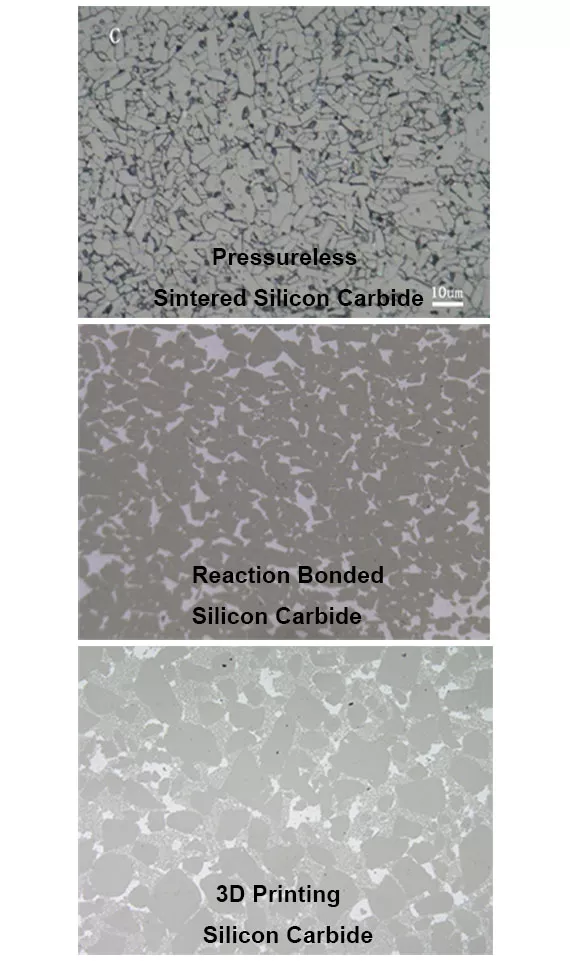
Customized Arm Material Parameters and Selection
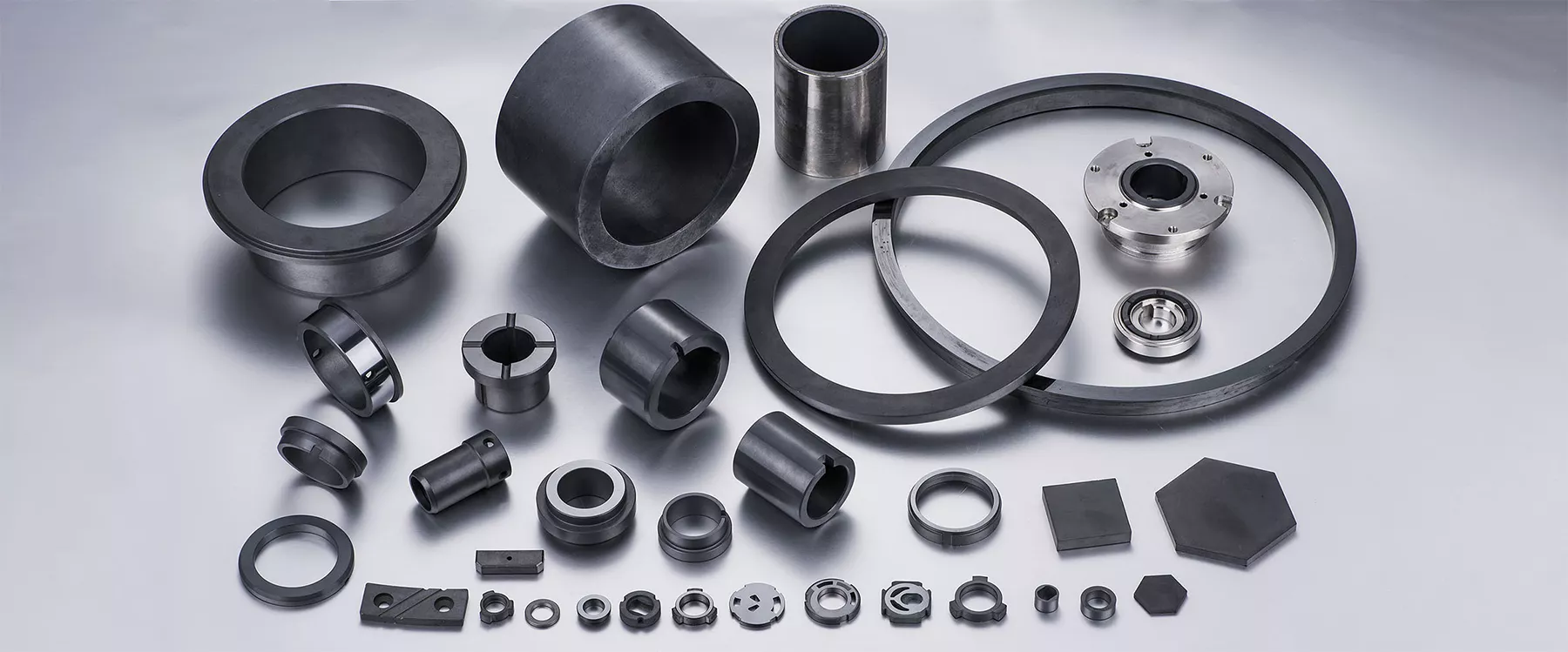
Pressureless sintered Silicon Carbide
Reaction-Sintered Silicon Carbide
3D Printing Silicon Carbide Ceramics
Find Silicon Carbide Ceramic Products for Your Application
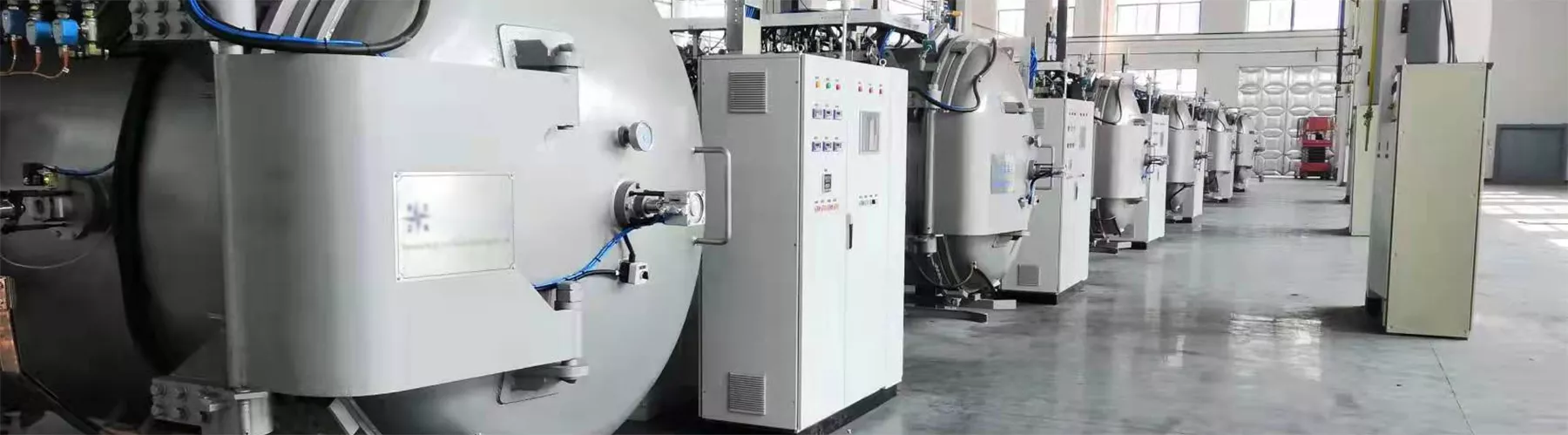
⬛Microchannel Reaction Products
As the core component of microchannel continuous flow chemical reactor/equipment, silicon carbide microchannel reactor can effectively solve your chemical application problems.
GORGEOUS can customize various microchannel reaction products for you: silicon carbide reaction tube, silicon carbide micro reaction plate, silicon carbide micro reaction module
⬛Corrosion-Resistant Heat Exchange Products
Silicon carbide ceramics are commonly used in processes such as cooling, condensing, heating, evaporating, thin-film evaporating and absorbing highly corrosive chemicals. Silicon carbide ceramics have better performance and higher overall benefits than traditional heat exchange equipment.
GORGEOUS can customize various corrosion-resistant heat exchange products for you: silicon carbide heat exchange plate, silicon carbide tube bundle block, silicon carbide tube sheet, silicon carbide heat exchange block hole, silicon carbide head, silicon carbide heat exchange tube, silicon carbide thermometer protection sleeve.
⬛High Temperature Resistant Products
GORGEOUS’s silicon carbide ceramics have extremely strong high temperature resistance and can withstand temperatures up to 1650°C, providing the best solution for your high temperature applications.
GORGEOUS can customize various high temperature resistant silicon carbide ceramic products for you: silicon carbide crucibles, silicon carbide thermocouple protection tubes, silicon carbide heat radiation plates, silicon carbide heat radiation tubes, reaction sintered silicon carbide burner sleeves, silicon carbide ceramic bushings, etc.
⬛Wear-Resistant Products
GORGEOUS can provide you with wear-resistant ceramic products, such as silicon carbide grinding liners, which have grinding structures and external heat exchange channels inside. The maximum outer diameter can reach 1300mm and the height can reach 1200mm, providing you with high grinding efficiency.
GORGEOUS can also provide you with customized other wear-resistant products: 3D printed grinding discs, silicon carbide desulfurization nozzles, silicon carbide impellers, silicon carbide sandblasting nozzles, silicon carbide sulfuric acid atomization nozzles, silicon carbide grinding cylinders, etc.
⬛Ion Etching Resistant Products
GORGEOUS can provide you with customized ceramic carrier structures suitable for ICP etching process, PVD process, RTP process, and CMP process in the manufacture of optoelectronic lighting epitaxial wafers.
GORGEOUS can customize ion-etching resistant silicon carbide ceramic products for you: silicon carbide PVD carrier, silicon carbide ICP carrier
⬛Heat Shock Resistant Products
GORGEOUS can provide you with customized products for heat shock resistant applications: silicon carbide cantilever slurry, silicon carbide cantilever beam, silicon carbide boat support, silicon carbide air pipe, silicon carbide RTA carrier, etc.
⬛High-Purity Products
GORGEOUS can provide you with ultra-high purity silicon carbide ceramics, with a base material purity of up to 99.99%, a surface silicon carbide coating purity of up to 99.999%, and a high temperature resistance of up to 1650°C, ensuring the stability of your high-temperature applications.
GORGEOUS can customize high-purity silicon carbide products for you: silicon carbide furnace tubes, silicon carbide coating discs for silicon epitaxy, silicon carbide cantilever slurries
⬛Armor Protection Products
Silicon carbide has extremely high hardness and is widely used in armor systems.s.
GORGEOUS can provide you with customized protective ceramics: silicon carbide bulletproof inserts, SIC bulletproof sheets, etc.
Application Fields of Silicon Carbide Ceramics
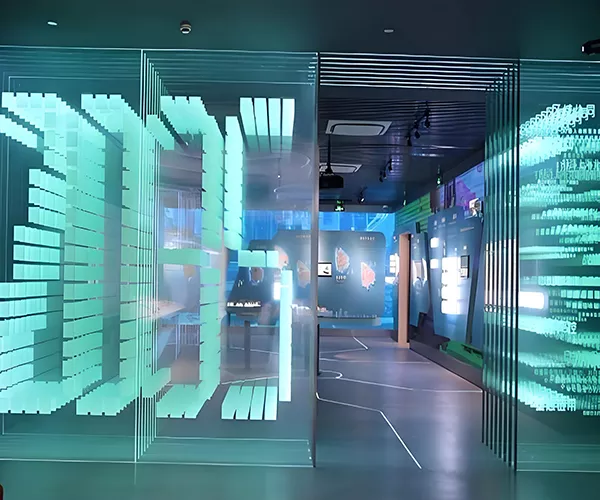
Electronic Glass
Silicon carbide has excellent high temperature properties (strength, oxidation resistance, low creep), high density, low porosity, and low impurities. It is an ideal material for heat-resistant components in the electronic glass forming process. It is often used in glass hot bending machines, aspheric glass molding machines and other equipment, such as silicon carbide ceramic heat sinks, silicon carbide mold sleeves, silicon carbide molds, silicon carbide heating plates, etc.
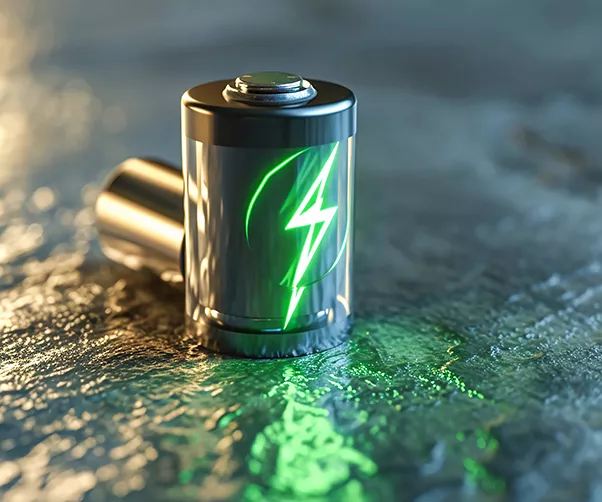
Battery Materials
Rollers and square beams made of silicon carbide are widely used in sintering kilns for positive and negative electrode materials of lithium batteries. In addition, silicon carbide wear-resistant parts with extremely high hardness and strength can also be used in powder processing equipment such as sanding and dispersion of lithium battery materials. Common silicon carbide ceramic products used in the battery material industry include silicon carbide square beams and semi-open square beams, silicon carbide rollers, silicon carbide furnace tubes, silicon carbide grinding cylinders, etc.
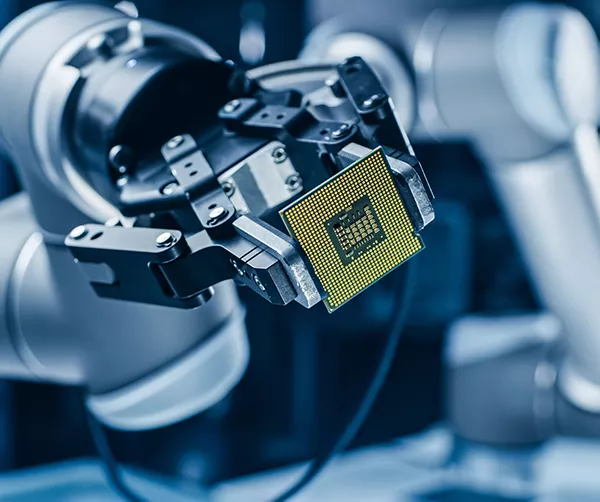
Semiconductor
Silicon carbide ceramic materials have high strength, high hardness, high elastic modulus, high thermal conductivity, low thermal expansion coefficient, etc., as well as good specific stiffness and optical processing performance, and are particularly suitable for some precision accessories of semiconductor equipment. For example, they are used in photolithography machines, wafer handling robots, etc. Commonly used silicon carbide products include silicon carbide cantilever slurry, silicon carbide ring chuck, silicon carbide chuck, silicon carbide vacuum chuck, silicon carbide robotic arm, etc.
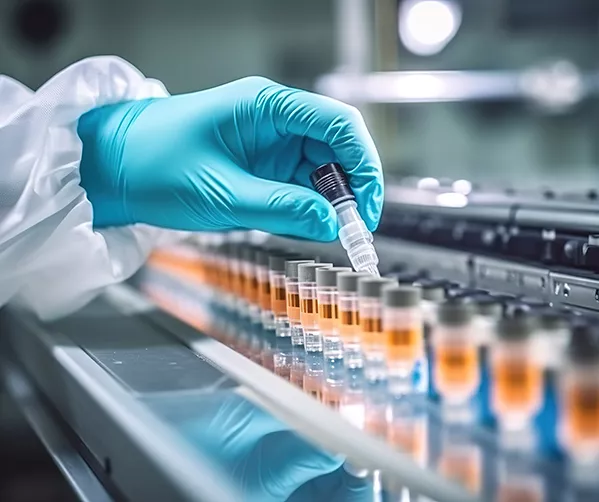
Chemical and Pharmaceutical
Silicon carbide ceramics are very suitable for cooling, condensing, heating, evaporation, thin film evaporation and absorption equipment for highly corrosive chemicals. Compared with traditional heat exchange equipment, silicon carbide heat exchange equipment has better heat exchange efficiency, so it is more compact, small in size, easy to disassemble and has low maintenance costs. Common silicon carbide ceramic products include silicon carbide tube bundle blocks, silicon carbide heat exchange block holes, silicon carbide heads, silicon carbide heat exchange tubes, etc.
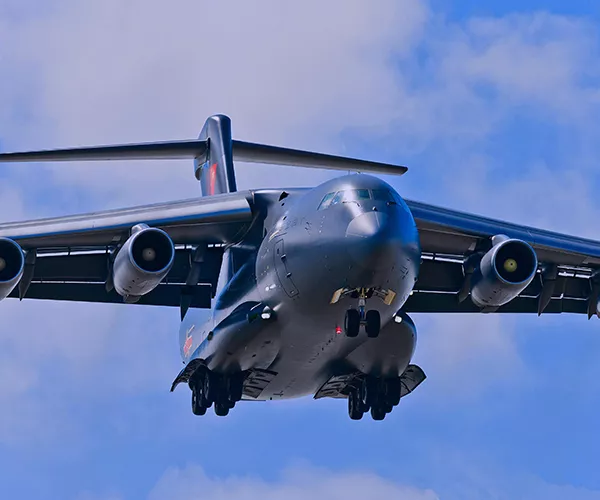
Food and Pharmaceutical Industry
Ceramic materials do not contain metal ion precipitation and are suitable for fields such as food processing and pharmaceutical packaging that require extremely high material cleanliness.
One-stop silicon carbide ceramic manufacturing service
15+ Years of Experience. High Precision and OEM Design. Professional R&D Team. Competitive Price.
What are the main advantages of silicon carbide (SiC) ceramics compared to other materials?
Silicon carbide ceramics provide excellent performance for demanding applications.
- High temperature resistance - (up to 1650°C) ideal for furnace components or aerospace
- Extremely high hardness (Mohs hardness 9.5) better than alumina and zirconia
- Chemically inert, resistant to acid and alkali corrosion
- Thermal conductivity is better than most heat exchanger ceramics
Can SiC ceramics be machined into complex shapes?
Yes, sintered SiC forms near net shapes during sintering; post-machining requires diamond tools (costly); reaction bonded SiC allows more machining flexibility before final sintering; 3D printing, an emerging technology for prototyping.