Ceramic Substrate Manufacturers
Ceramic substrates have excellent electrical insulation properties and are often used in the electronic and electrical fields.Application: Industrial, Renewable and Vehicle Electrification
Best cost&performance ratio!
Customized Supply of Ceramic Substrates
Ceramic substrates are primarily used in modern electronic systems. GORGEOUS provides customized solutions using ceramic substrates such as alumina, aluminum nitride, zirconium oxide, silicon nitride, and silicon carbide.
We offer all common ceramic substrates on the market, providing a one-stop service. In addition to ceramic substrates, we also provide thin-film circuit fabrication, laser processing, and metallized substrate services, enabling us to manufacture high-quality thin-film ceramic substrates and ceramic substrate PCBs. Contact us to find the solution that best meets your needs.
Customizable Ceramic Substrate Material
Various materials for you to choose!
We provide the best material recommendations based on your application requirements and customize the most suitable ceramic substrates, thick film ceramic PCBs, etc.
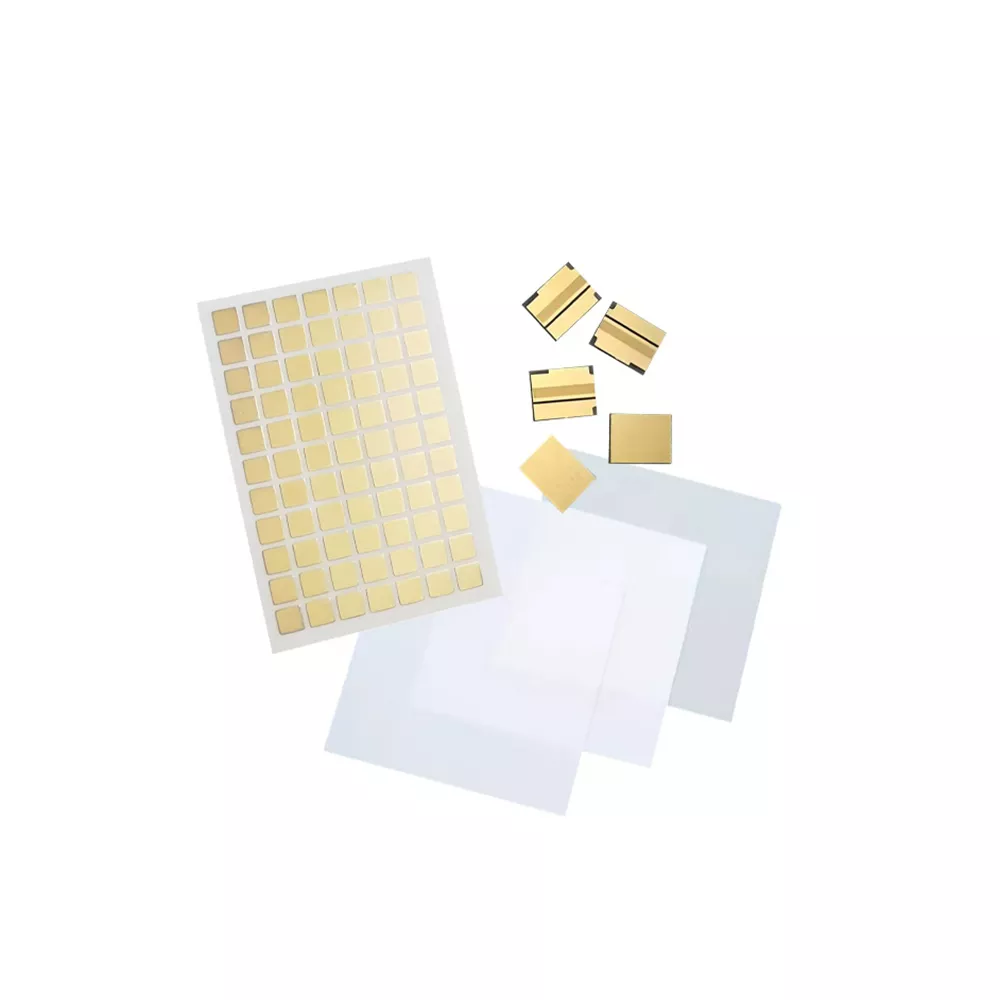
Alumina Substrate
The most commonly used ceramic substrate in industrial, renewable energy, automotive electrification, and high-performance electronics. Customizable. Send us a message to get a quote.
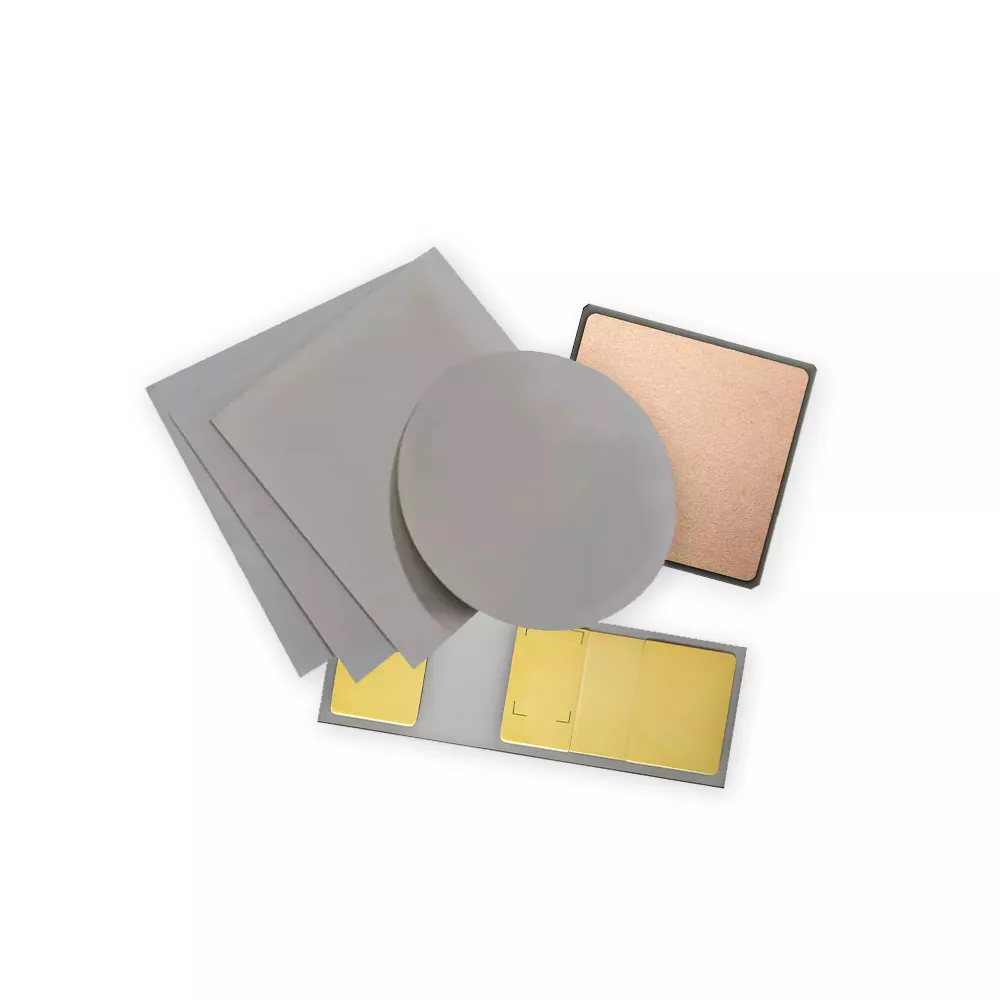
AlN Substrate
AlN boasts high thermal conductivity and a CTE very close to that of silicon, making it primarily used in trains, industry, renewable energy, and LEDs. Customization is available; send a message to receive a quote.
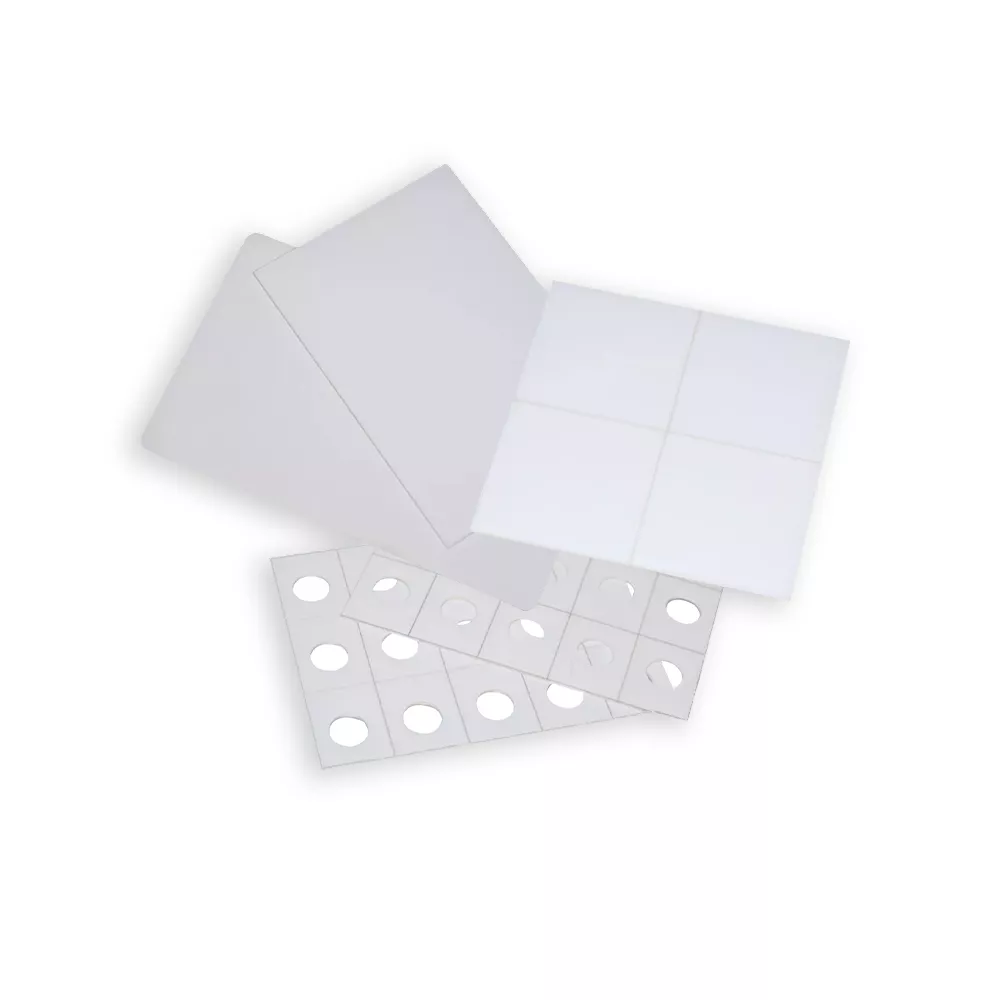
Zirconia Substrate
It has high flexural strength and high fracture toughness, making it ideal for heating and sensor, automotive applications. Customization is possible, please send a message to receive an inquiry.
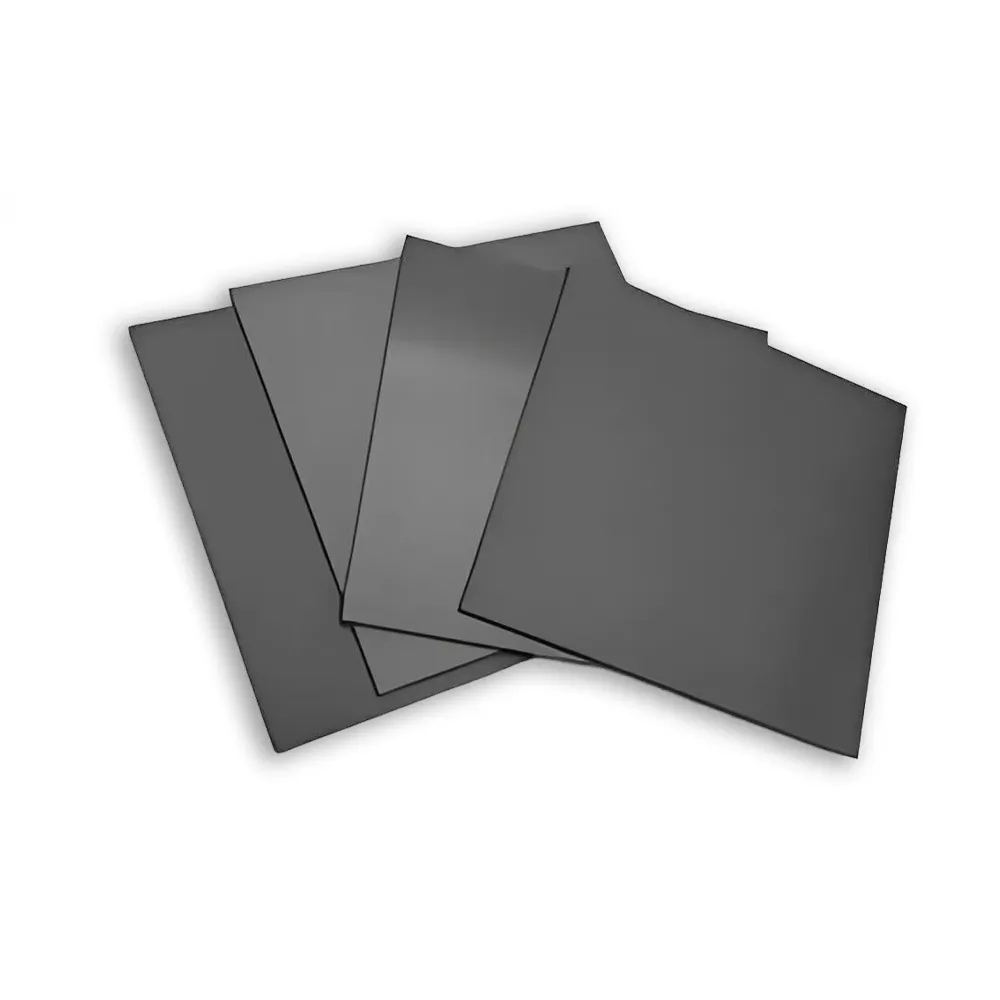
Silicon Nitride Substrate
High flexural strength, high fracture toughness, and good thermal conductivity make it suitable for electric vehicles and industrial applications. Send a message to receive an inquiry.
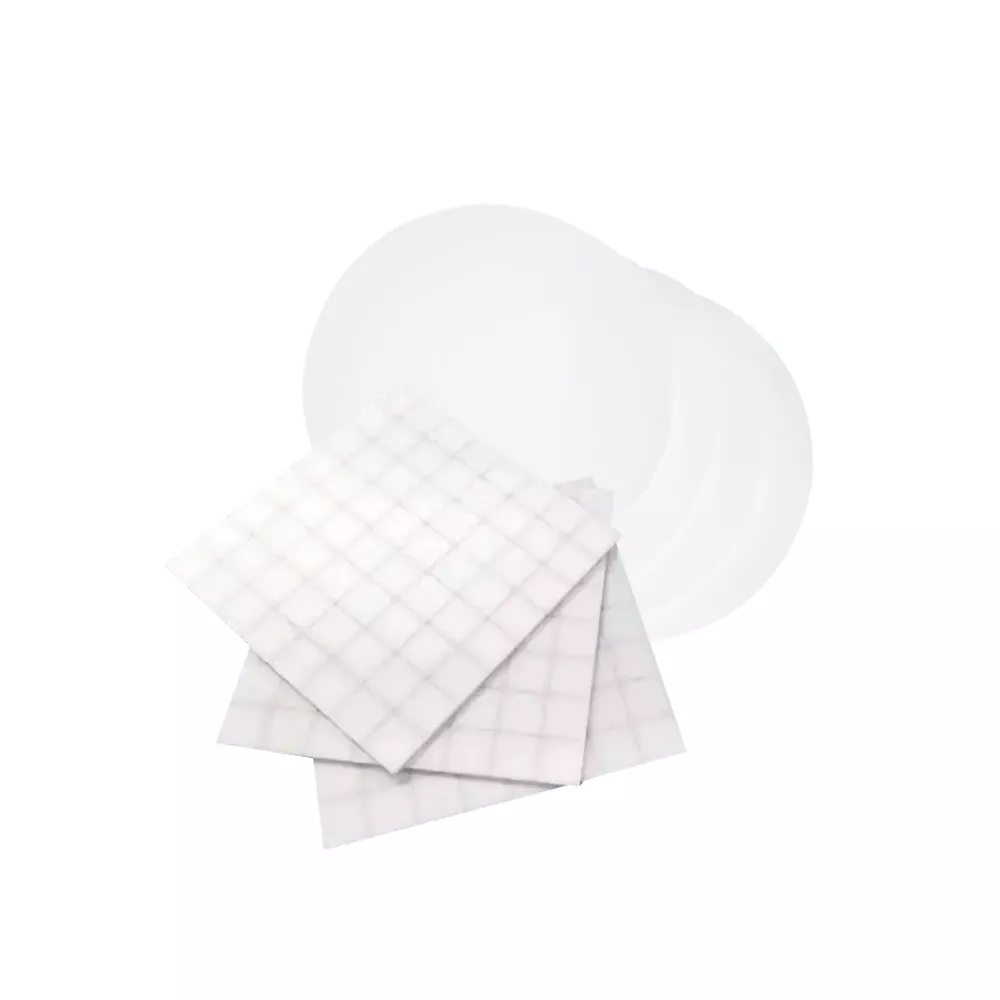
Beryllium Oxide Substrate
It has exceptionally high thermal conductivity and heat dissipation capabilities, and our company is capable of safely and compliantly processing it. Send us a message to get a quote.
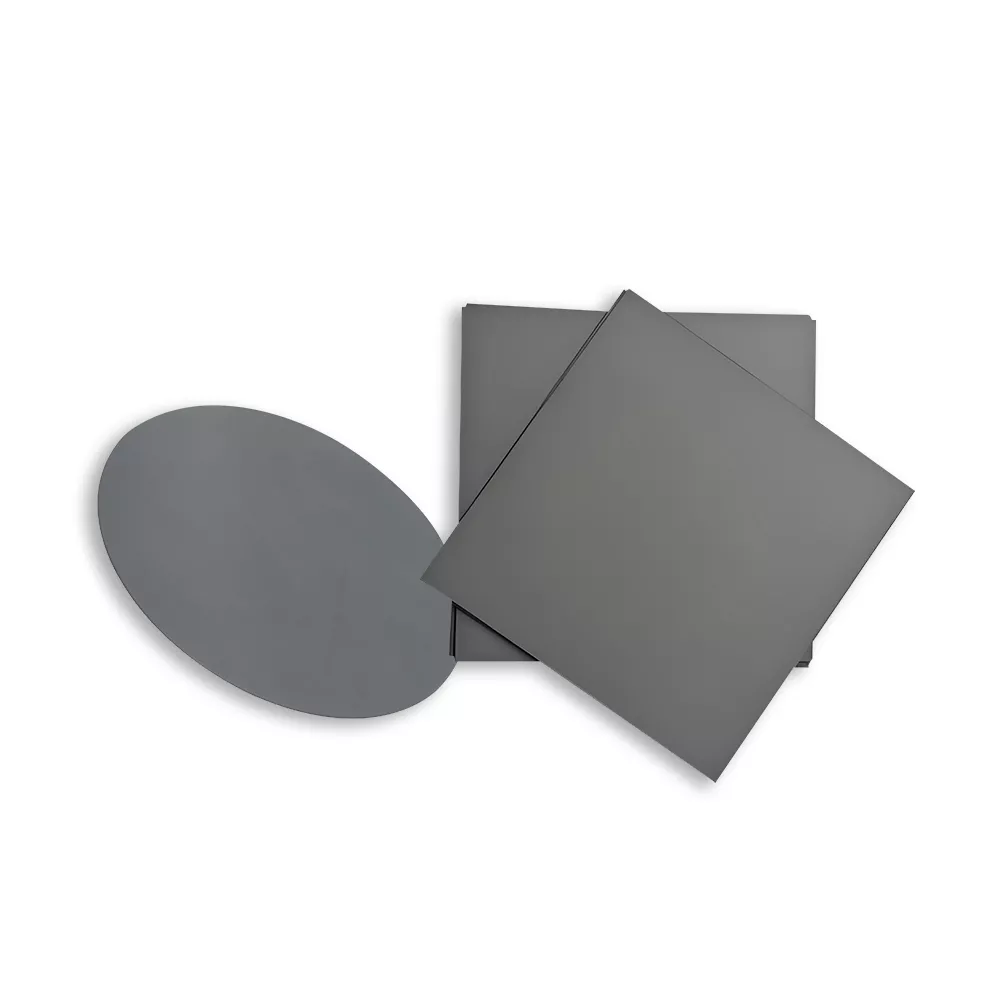
Silicon Carbide Substrate
Ultra-high thermal conductivity and excellent mechanical properties make it ideal for power electronics, 5G base stations and RF devices, LEDs, and more. Send us a message to get a quote.
Standard Size of Substrate
Substrate Size (mm) | Dimensional Error (mm) |
50.8*50.8 | ±0.2 |
76.2*76.2 | ±0.3 |
101.6*101.6 | ±0.4 |
Substrate Thickness
The substrate thickness is 0.1-3mm, with typical thicknesses of 0.254, 0.381, 0.508, and 0.635. The substrate thickness tolerance is ±10%.
thickness(mm) | Thickness tolerance (mm) | ||
As-fired | Ground | Polished | |
0.127 | ±0.012 | ±0.005 | ±0.005 |
0.254 | ±0.025 | ±0.005 | ±0.005 |
0.381 | ±0.038 | ±0.005 | ±0.005 |
0.508 | ±0.050 | ±0.01 | ±0.01 |
0.635 | ±0.063 | ±0.01 | ±0.01 |
0.762 | ±0.076 | ±0.01 | ±0.01 |
1.016 | ±0.10 | ±0.01 | ±0.01 |
Technical Capabilities
Substrate Type | Surface Roughness | Warpage |
As-fired |
Front: ≤100nm Back: ≤200nm |
0.3% |
Ground | According to customer requirements | 0.1% |
Polished | ≤25nm | 0.1% |
Laser and Metallized Substrates
At GORGEOUS, we offer a flexible selection of advanced manufacturing processes, including hard machining technologies like stamping, laser processing, and dry pressing, tailored to our customers’ needs based on application scenarios, material properties, geometry, and production batch sizes.
We provide high-precision metallization for our customers’ ceramic substrates, enabling them to be directly assembled with electronic components. Our proprietary metallization solder paste offers excellent adhesion and flow, ensuring a stable and reliable soldering process.
During the metallization process, a uniform conductive layer is formed on the surface of our substrates. This not only provides an efficient conductive path and reliable electrical connections for electronic components, but also effectively prevents corrosion and other environmental factors from affecting substrate performance.
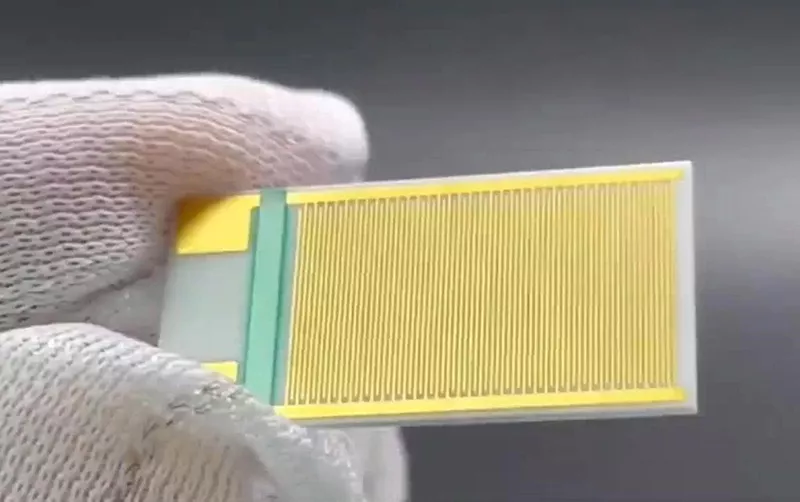
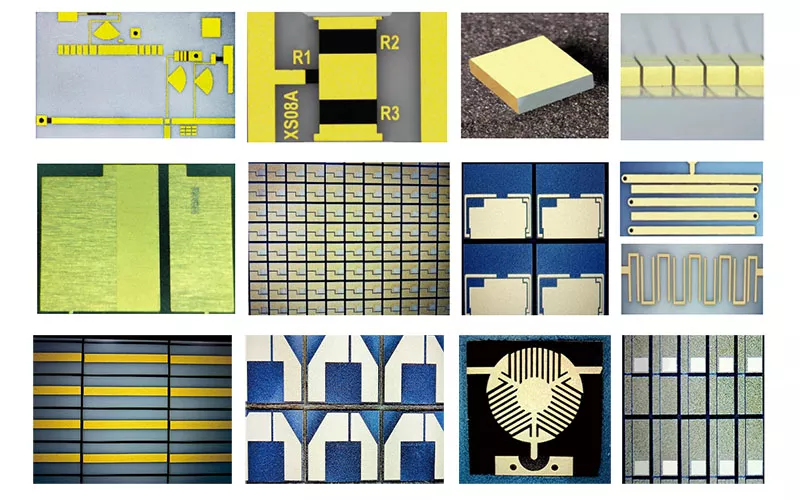
Thin Film Circuit Processing
GORGEOUS manufactures thin-film circuits for our customers. Our automated thin-film circuit production line provides one-stop thin-film hybrid integrated circuit solutions, encompassing materials, design, manufacturing, and application.
Applications for these thin-film hybrid integrated circuits are broad, including power dividers, couplers, microwave/millimeter-wave filters, microwave/millimeter-wave attenuators, ferrite circulators, microwave/millimeter-wave devices, laser diode packaging, high-density interconnects, and D/A-A/D converters.
If you need thin film ceramic substrates, ceramic substrate PCBs, or metallized ceramic substrates, please contact us immediately and we will provide you with the best customized service!
FAQ
What ceramic substrate materials does GORGEOUS offer?
We offer substrates made of alumina, aluminum nitride, silicon nitride, beryllium oxide, and silicon carbide. We also offer metallized ceramic substrates and thin-film circuit processing.
What are the differences between Al2O3, AlN, and Si3N4 substrates?
Aluminum oxide offers cost-effectiveness and good insulation properties; aluminum nitride offers excellent thermal conductivity; and silicon nitride offers strong mechanical strength, good thermal conductivity, and good insulation properties.
What applications are ceramic substrates used for?
Ceramic substrates are primarily used in electric vehicles, renewable energy, industry, aviation technology, power electronics, and other fields.
What metal bonding technologies do we support?
We support AMB (Active Metal Brazing), DCB (Direct Copper Bonding), and SMB (Sputtered Metal Bonding).