In the history of the development of human civilization, the earliest ceramic technology can be traced back to the Neolithic Age. From the original clay products, to exquisite porcelain, to modern engineering ceramics, ceramic technology is constantly innovating.
Ceramics are a type of inorganic non-metallic material, generally made by high-temperature sintering of compounds. Ceramic materials have excellent physical and chemical properties. From the earliest pottery to modern high-tech ceramic parts, the development of ceramic technology has witnessed the progress of human craftsmanship and technology step by step.
Are you curious about the difference between traditional clay ceramics and advanced ceramics? Reading this article will help you get the answer very well.
Quick Links
- What are Traditional Ceramics?
- Traditional Ceramic Manufacturing Technology
- Performance Characteristics of Traditional Ceramics
- Typical Applications of Traditional Ceramics
- What is Advanced Ceramics?
- Main Raw Materials for Advanced Ceramics
- Preparation Technology of Advanced Ceramics
What are Traditional Ceramics?
Traditional ceramics are fired from natural minerals such as clay, feldspar and quartz. This type of traditional ceramics has a very long history of development and is very mature in craftsmanship. Traditional ceramics are widely used in architecture, daily necessities and decoration in daily life. Common bowls, plates, vases and porcelain in our daily life are traditional ceramics.
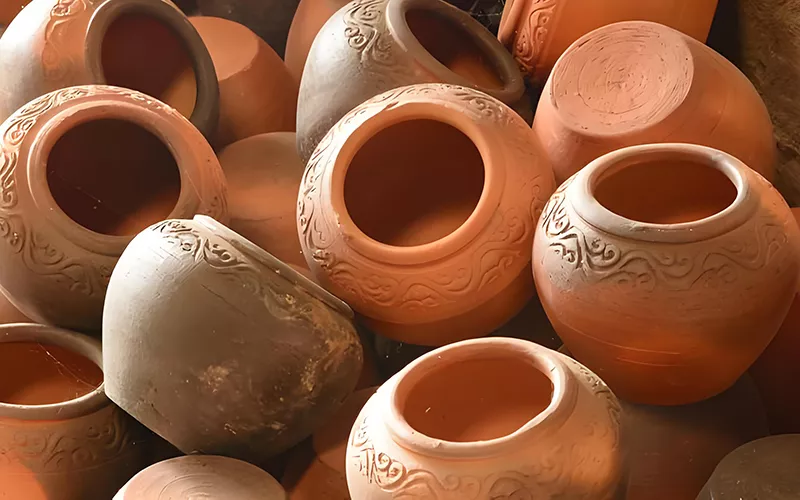
What are Traditional Ceramics
Traditional ceramics mainly use three natural raw materials:
Clay: Can provide greater plasticity and molding ability
Feldspar: Lower sintering temperature, which can promote densification
Quartz: Adjust thermal expansion coefficient and improve mechanical strength
Traditional Ceramic Manufacturing Technology
The production process of traditional ceramics is relatively simple and very mature. It is mainly divided into the following major steps:
- Raw material processing: crushing, screening and batching of raw minerals
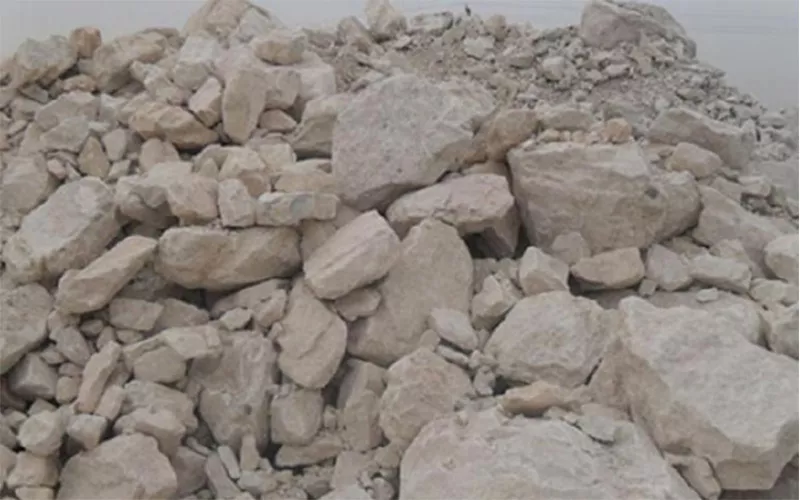
Untreated ceramic raw materials
- Molding: Using the plasticity of clay for molding or slip casting
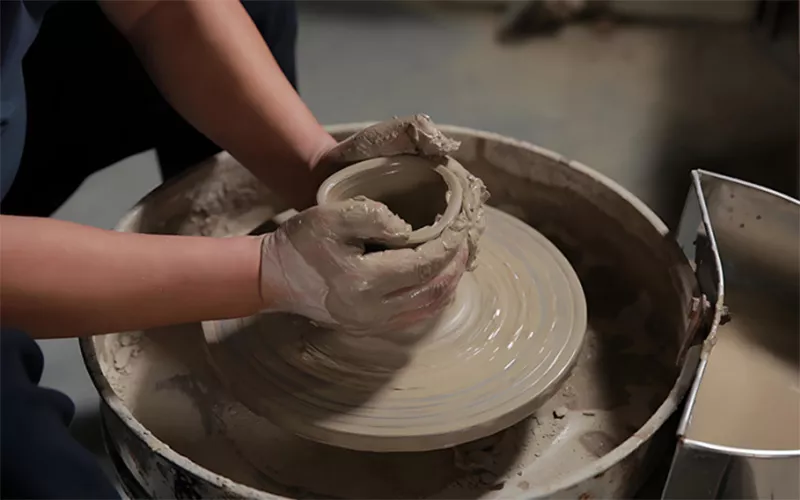
Shaping the Ceramic Jar
- Drying: Remove moisture from the green body to prepare for subsequent firing
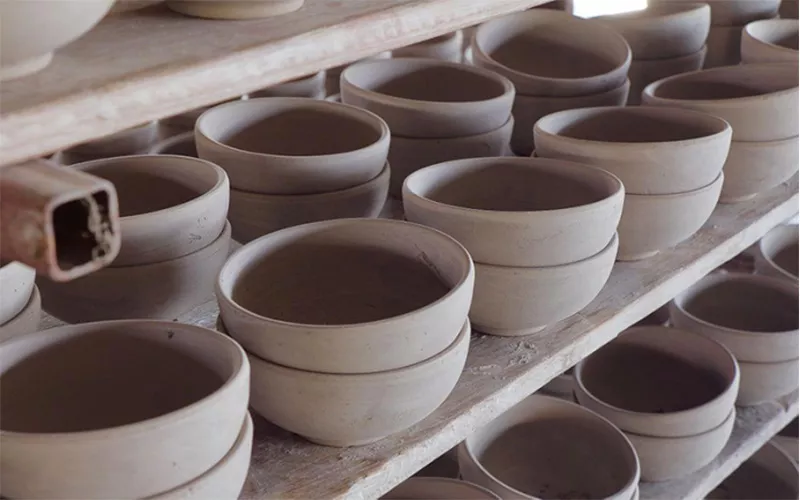
Ceramics waiting to dry
- Sintering: Sintering at high temperature in a high temperature kiln
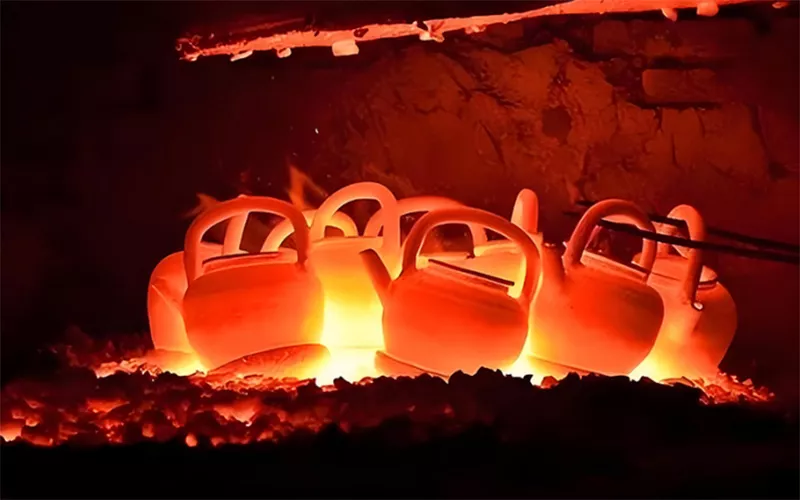
Firing ceramics
Performance Characteristics of Traditional Ceramics
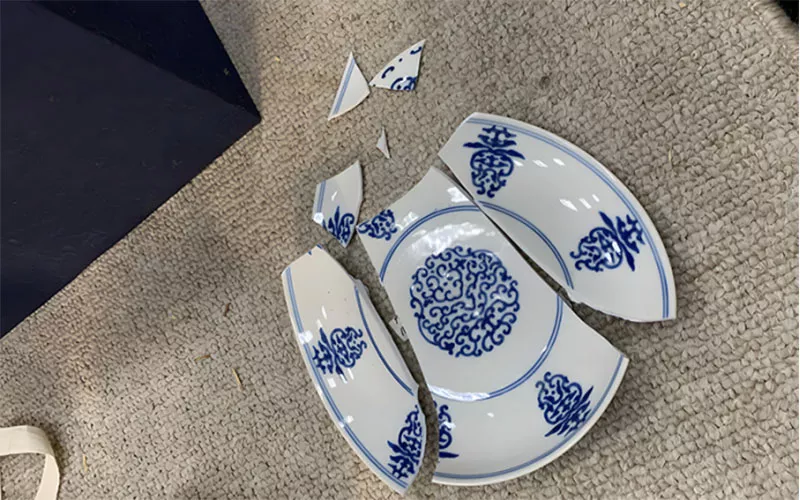
Ceramics are brittle and break easily
The performance of traditional ceramics is relatively general and they are mainly used in daily life. They have moderate hardness, are relatively brittle, can withstand general high temperatures, and have good insulation properties, making them perfect for use in infrastructure supplies and decorative artworks in life.
Typical Applications of Traditional Ceramics
Building materials: Bricks, tiles used in the construction industry
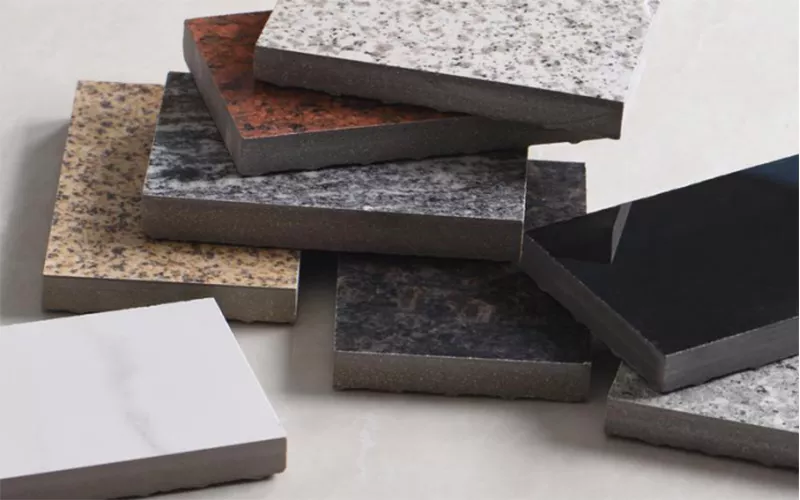
Ceramic imitation stone brick
Daily utensils: tableware and vases for daily life
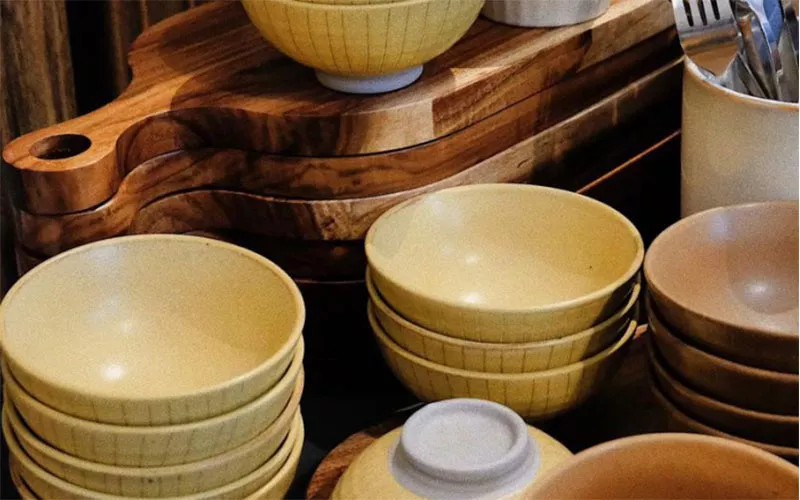
Ceramic tableware
Industrial use: some can be used for basic insulators and grinding materials
What is Advanced Ceramics?
Advanced ceramics, also known as engineering ceramics and special ceramics, are high-purity compounds and new high-performance ceramic materials prepared through modern process technology.
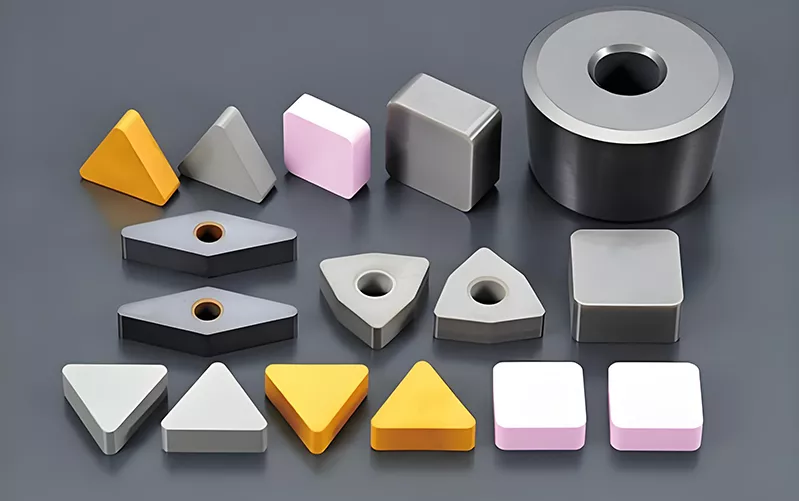
Advanced Ceramics
Ceramics made from different ceramic materials have different performance characteristics. The raw materials of advanced ceramics are usually refined compounds, such as various oxides, nitrides, etc. These high-purity compounds have very high consistency and stability, and are irreplaceable materials for various demanding applications.
Main Raw Materials for Advanced Ceramics
-
Oxides: Alumina (Al2O3), Zirconium Oxide (ZrO2), Beryllium Oxide (BeO)
Alumina ceramic:This is the most common advanced ceramic and one of the most cost-effective ceramics. It has strong comprehensive properties, high hardness, high temperature resistance, and electrical insulation. It is the preferred material for many applications.
Commonly used in refractory materials, insulating components, substrates, abrasives
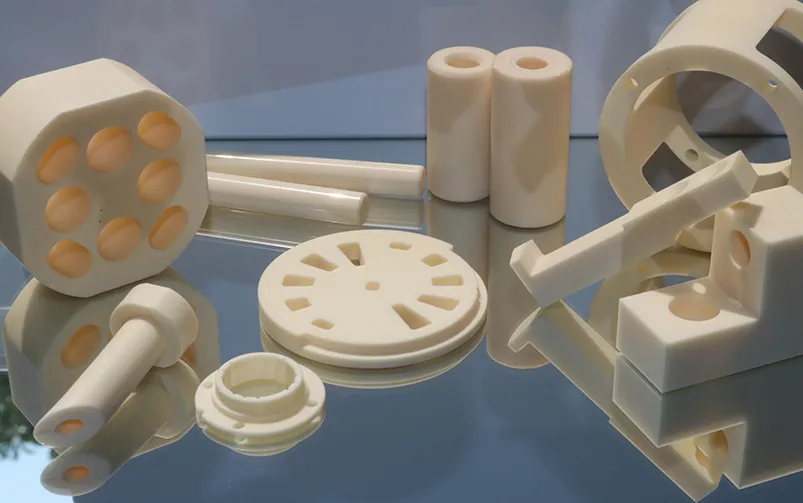
Alumina ceramic
Extended reading: Is aluminum oxide poisonous?
Zirconia ceramic:Its toughness is among the best among many ceramics, its strength is very high, and it is biocompatible and compatible with the human body. It is a commonly used ceramic material in dental applications.
Commonly used in ceramic knives, dental applications, wear parts, substrates
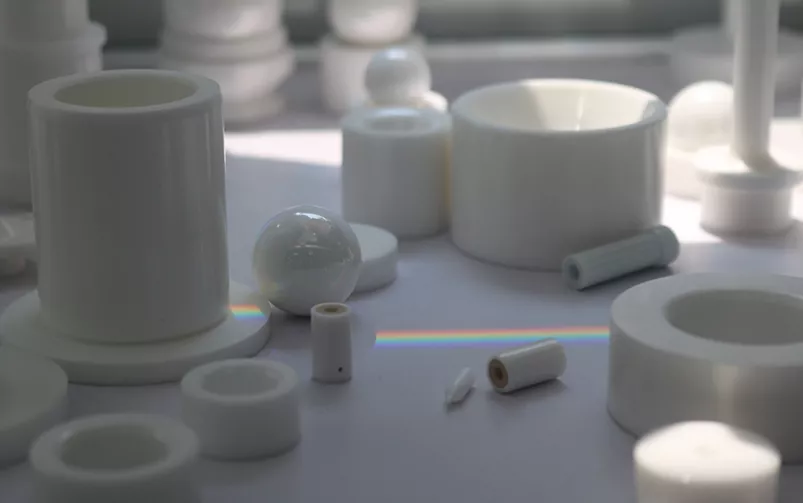
Zirconia ceramic
Extended reading: What are the uses of zirconia ceramics?
Beryllium oxide ceramic:Its thermal conductivity is outstanding and is one of the best thermal conductors among known ceramic materials. In addition, it can also be used as a moderator and reflector material for nuclear reactors. It is very useful in nuclear applications. However, it should be noted that beryllium oxide raw materials are usually toxic and special care must be taken during manufacturing.
Commonly used for substrates, wear-resistant parts, and high-temperature parts
Extended reading: What are the ceramic materials with the best thermal conductivity?
-
Non-oxides: silicon carbide (SiC), silicon nitride (Si3N4), aluminum nitride (AlN), boron carbide (B4C)
Silicon nitride ceramic:It has strong impact resistance and high temperature oxidation resistance, and is often used in some high-strength parts at extreme temperatures, such as automobile engine parts, turbine blades, bearings, etc.
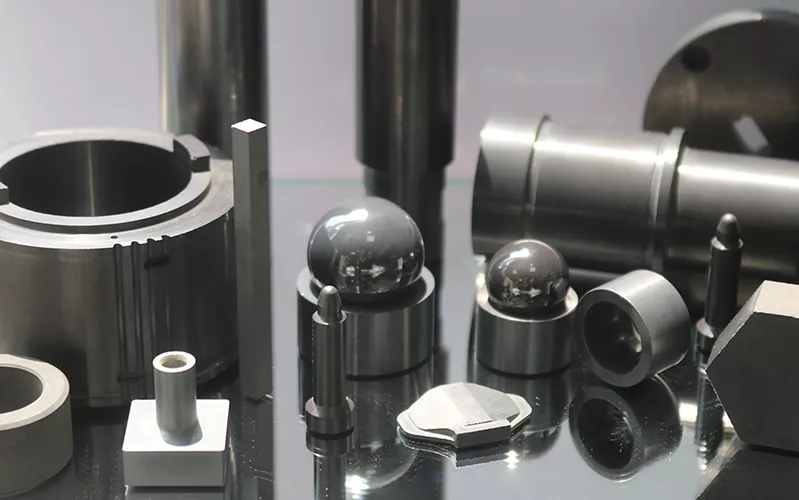
Silicon nitride ceramic
Extended reading: Uses of silicon nitride ceramics
Silicon carbide ceramic:It is one of the hardest ceramics, second only to diamond in hardness, and is known as “black diamond”.
Commonly used in semiconductor substrates, chemical equipment components, and bulletproof materials
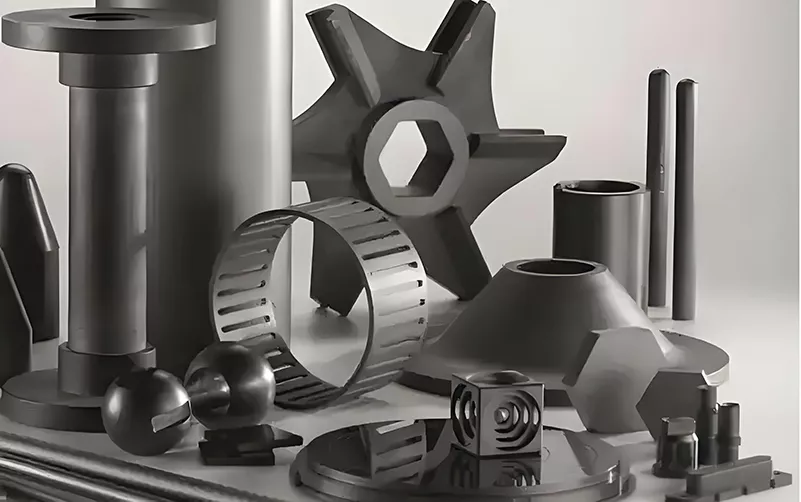
Silicon carbide ceramic
Extended reading: What are the uses of silicon carbide ceramics?
Aluminum nitride ceramic:The thermal conductivity of aluminum nitride is also excellent, and it is one of the best ceramic materials. It can be used as a heat dissipation material for most high-power electrical appliances.
Commonly used for heat dissipation substrates and heat dissipation components
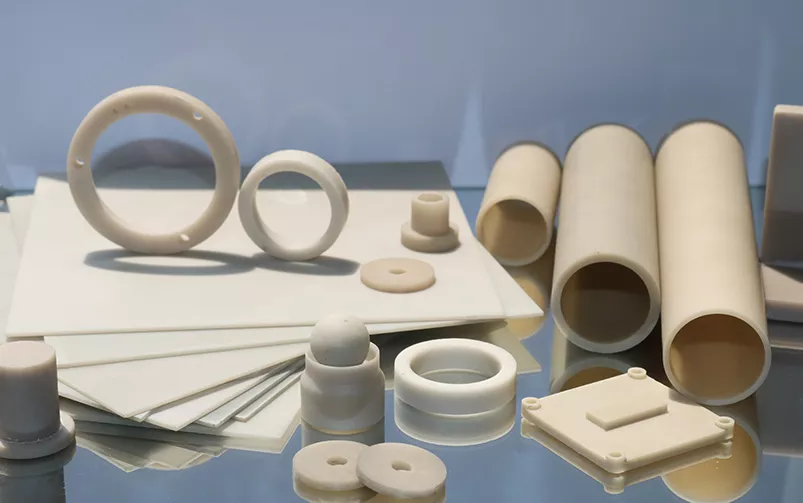
Aluminum nitride ceramic
Boron carbide ceramic:This is an excellent bulletproof material, known as the “lightest bulletproof ceramic”. Its density is smaller than that of ordinary ceramic materials, and its protective performance is strong. In the US military, many small arms protection inserts use boron carbide ceramic plates.
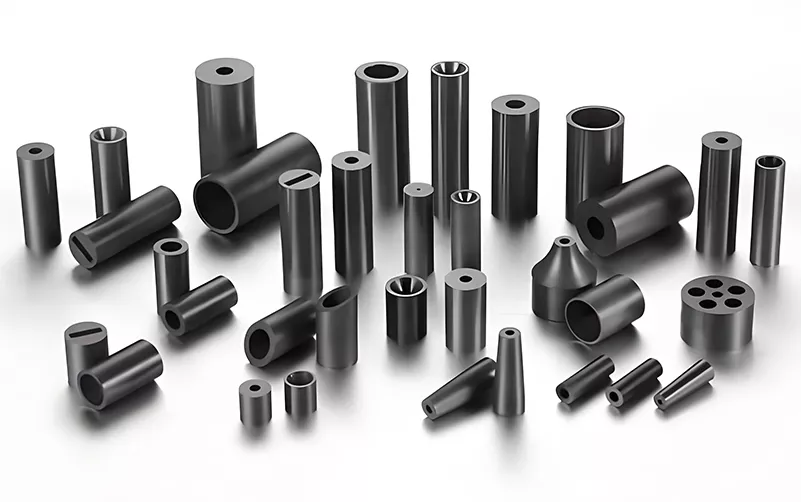
Boron carbide ceramic
Extended reading: Application of boron carbide in bulletproof
-
Composite materials: Ceramic matrix composites
Composite ceramics are made of a variety of ceramic materials, combining multiple superior properties and making up for each other’s shortcomings. The most common ones are zirconia-reinforced alumina ceramics (ZTA) and yttria-stabilized zirconia (YSZ), one of which enhances the toughness of alumina and the other makes the original zirconia more stable.
Preparation Technology of Advanced Ceramics
Compared with traditional ceramics, the preparation process of advanced ceramics is more complex and precise, and requires the use of a variety of technical equipment. The main steps are as follows:
- Powder synthesis: Processing ceramic raw materials into ultrafine powders
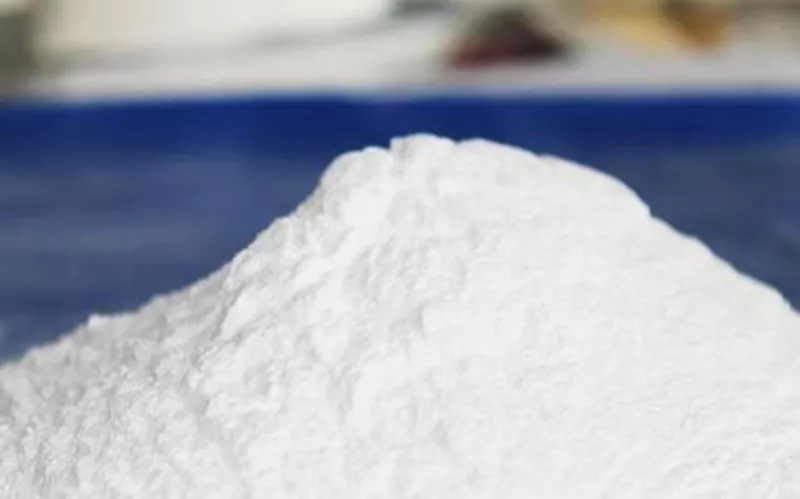
Ceramic powder
- Molding: Molding using isostatic pressing, injection molding and other methods
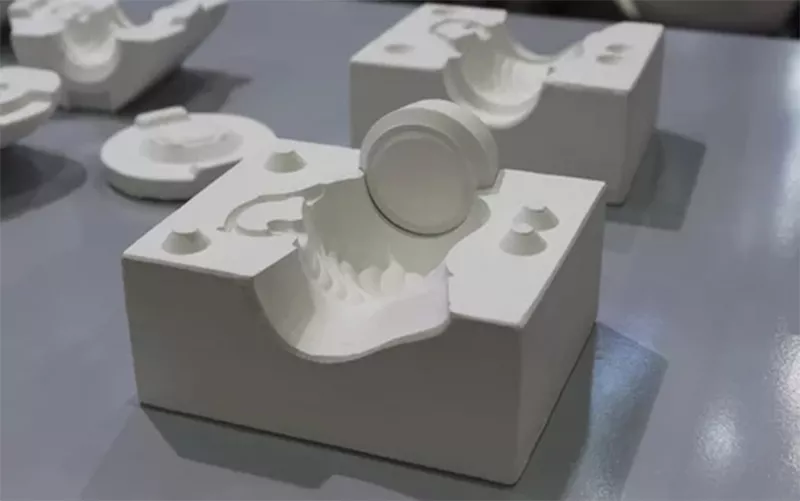
Ceramic Injection Molding Molds
- Sintering: High temperature sintering with precise temperature control
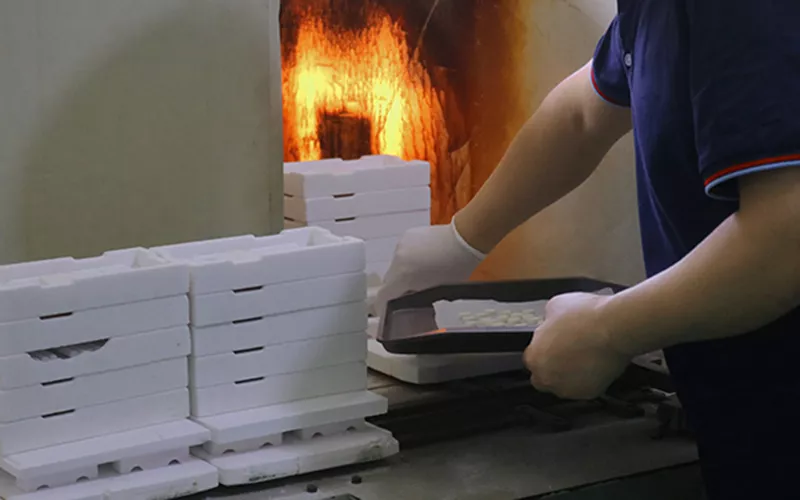
Advanced ceramic sintering
- Post-processing: Finally, a series of precision processing and surface treatment are carried out
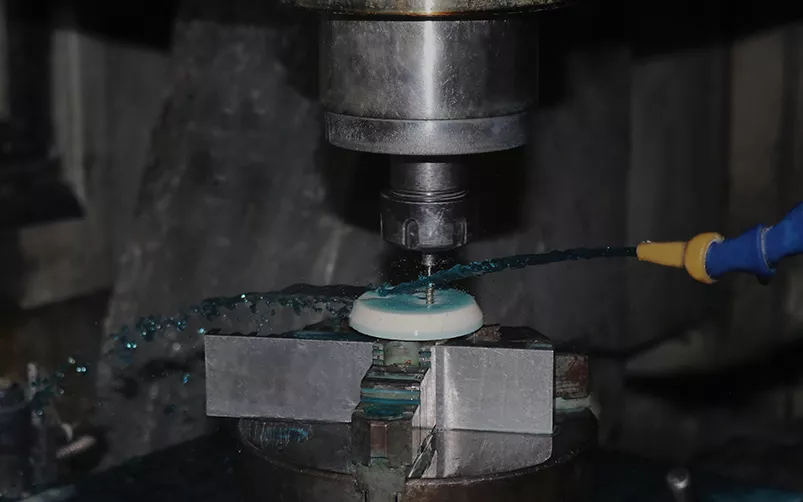
Ceramic precision machining
Advanced Ceramics Performance Parameters Table
We have drawn up performance parameter tables of various advanced ceramic materials for your reference
Performance |
Unit |
Al₂O₃ |
ZrO₂ |
BeO |
AlN |
Si₃N₄ |
SiC |
B₄C |
Density |
(g/cm3) |
3.95-4.1 |
5.6-6.1 |
3.0 |
3.26 |
3.2-3.3 |
3.1-3.3 |
2.5-2.6 |
Compressive strength |
(MPa) |
1500-2000 |
1200-1300 |
1700-2000 |
1700-2000 |
1700-2200 |
2500-3000 |
3000-3500 |
Bending strength |
(MPa) |
200-400 |
900-1200 |
400-600 |
350-600 |
1000-1500 |
400-600 |
400-600 |
Fracture toughness |
(MPa·m^1/2) |
250-350 |
500-600 |
300-450 |
200-400 |
800-1200 |
600-800 |
500-700 |
Coefficient of thermal expansion |
(10⁻⁶/K) |
3-4 |
8-10 |
3-4 |
3.5-4 |
6-7 |
4-5 |
3-4 |
Thermal conductivity |
(W/m·K) |
7.9-9 |
2.2-2.5 |
200-250 |
180-220 |
30-35 |
120-150 |
30-50 |
Melting point |
(℃) |
2050 |
2700 |
2500 |
2200 |
1900 |
2700 |
2500 |
Conclusion
Traditional ceramics continue to play an important role in basic applications in life with their mature technology and economy, while advanced ceramics promote the development of high-tech industries with their excellent performance. Thank you for reading this article, I hope it can help you.
Learn more about ceramic materials