Ceramic crucibles are containers specifically designed for use in extreme temperature applications, most commonly used in metal melting and chemical applications.
Introduction to Ceramic Crucibles
Ceramic crucibles can be made of various ceramic materials, and each type of ceramic crucible has its own unique characteristics. As the main tool for smelting metals, conducting chemical experiments and processing high-temperature materials, crucibles need to have extremely strong high-temperature resistance and corrosion resistance, and ceramic materials just meet these requirements.
What Are The Materials of Ceramic Crucible?
Alumina Crucible
The main raw material of alumina crucible is 99.7% high-purity alumina, in addition to which it usually contains a small amount of magnesium oxide (MgO) and silicon dioxide (SiO2). Under the action of these ingredients, it has many excellent physical and chemical properties.
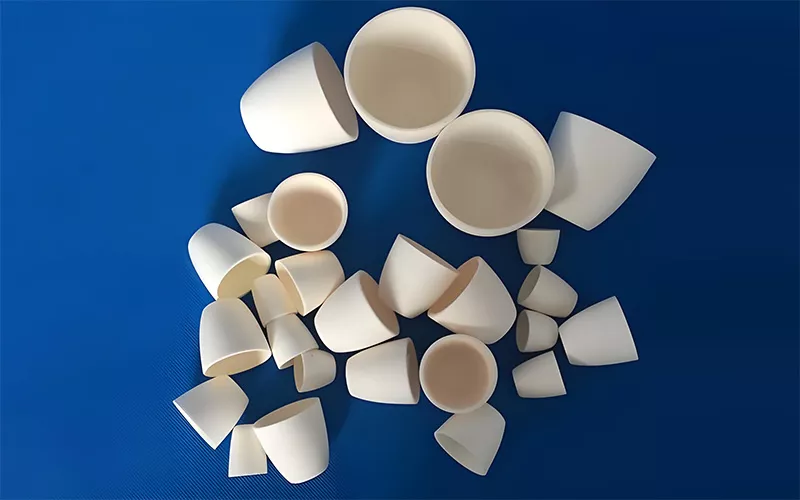
Alumina Crucible
Due to its high temperature resistance, alumina crucibles are widely used in some laboratories and industries. Especially in some smelting, heating and chemical reactions under high temperature environments, it can often be seen.
The cost of alumina crucible is low, and it is also one of the most common and high-demand crucible products on the market. Normally, alumina crucibles can withstand high temperatures from 1650°C to 1700°C in a redox atmosphere, and are very suitable for high-temperature processing of melting applications of various materials, especially for processing some weakly alkaline materials, such as anhydrous sodium carbonate (Na₂CO₃) etc., alumina crucible performs very well.
The high melting point and low thermal expansion coefficient of alumina give the crucible excellent heat resistance and stability, which allows it to maintain its shape and structure integrity during the smelting process and is not prone to cracks. The superior chemical inertness of alumina also makes it difficult to react with most chemical substances.
However, you need to note that it is not suitable for melting certain highly corrosive substances, such as strong alkaline substances such as sodium hydroxide (NaOH) and sodium peroxide (Na2O2). In this case, the alumina crucible may be severely corroded. Therefore, we recommend that you choose other more corrosion-resistant crucible materials to handle these substances.
Zirconia Crucible
Zirconia crucibles are made of high-purity zirconium oxide (ZrO₂). They have excellent high-temperature resistance and are a good choice for some high-temperature applications. Zirconia crucibles can withstand temperatures up to 2000°C and are often used for material melting applications at extreme high temperatures, such as melting some precious metals such as platinum (Pt), palladium (Pd), and ruthenium (Ru). These metals have high melting points and very strict requirements on the materials of the crucible, and zirconia crucibles have become the first choice for melting them.
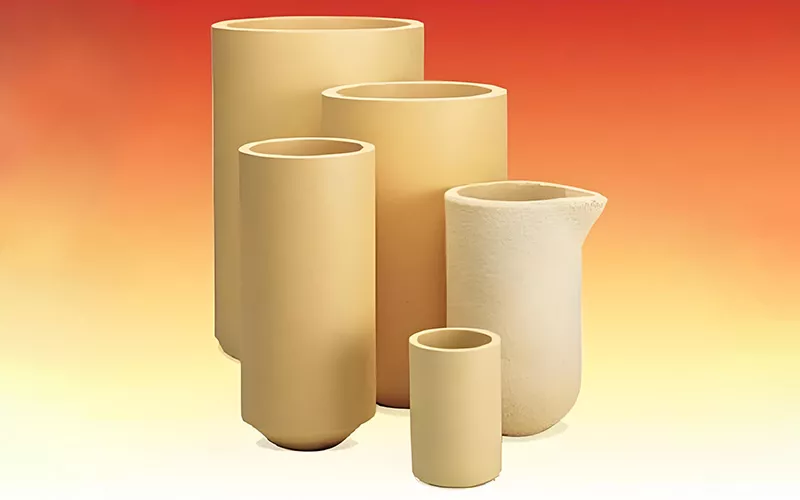
Zirconia Crucible
Compared with alumina crucibles, the cost of zirconia crucibles is higher because zirconia raw materials are more scarce than alumina and the processing technology is more complicated. Although zirconia is more expensive, zirconia crucibles have stronger high temperature resistance and chemical stability than alumina crucibles, especially for some high melting point metals, zirconia crucibles can better withstand the extreme temperature environment in the reaction.
In addition, the chemical corrosion resistance of zirconium oxide also enables it to maintain stability in strong acid, strong alkali and other harsh atmospheres, which also provides a favorable guarantee for the melting of precious metals. Therefore, for some high-temperature processes that need to handle precious metals or other high-melting-point, volatile materials, zirconium oxide crucibles are your ideal choice.
Zirconia Toughened Alumina Crucible (ZTA Crucible)
Alumina toughened alumina (ZTA) crucible is a high toughness crucible made of 90% high purity alumina and 10% zirconium oxide (ZrO₂). ZTA crucible combines the advantages of alumina and zirconium oxide. It has the excellent high temperature resistance of alumina and the excellent toughness of zirconium oxide.
Alumina itself has a very strong high temperature resistance and can withstand high temperatures of 1650℃-1700℃, while zirconium oxide improves the crack resistance and wear resistance of the crucible in high temperature environments. ZTA crucible relies on the advantages of these two materials to perform particularly well in some applications with harsh mechanical strength and temperature.
The significant improvement in toughness can ensure the crucible’s resistance to thermal shock and effectively avoid common cracks and breakages under extreme temperature changes. Compared with pure alumina crucibles, ZTA crucibles can better resist the stress caused by thermal expansion and have better coping methods in the face of sudden temperature changes.
Boron Nitride Crucible (PBN Crucible)
Boron nitride (PBN) is a crucible material that performs very well in high temperature environments. Crucibles made of it can be widely used in semiconductor manufacturing, metal smelting and other high-temperature processes. Boron nitride, as the main component of the crucible, gives the crucible excellent high temperature resistance, chemical stability and thermal conductivity. Under the protection of the atmosphere, the boron nitride crucible can remain stable at high temperatures up to 2100°C.
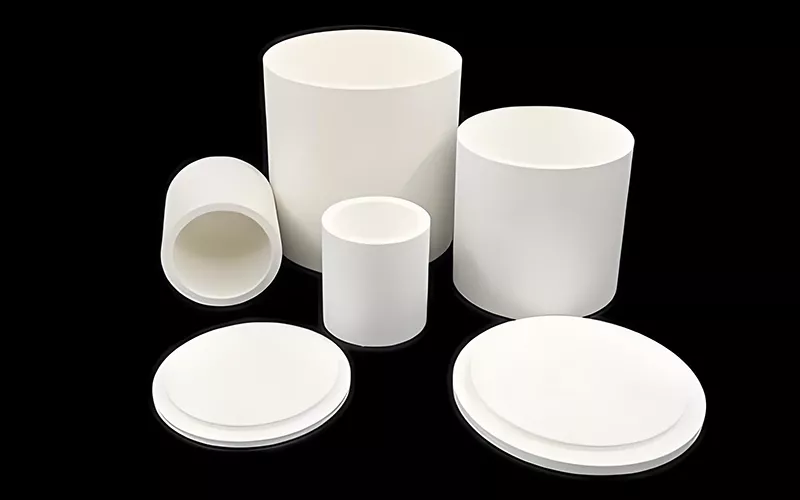
Boron Nitride Crucible (PBN Crucible)
The biggest advantage of boron nitride crucible is that it will not undergo obvious chemical reactions or melt even in extremely high temperature environments, and can meet your long-term high-temperature operation. In addition, the good thermal conductivity of boron nitride can effectively disperse heat at high temperatures, avoid excessive concentration of high temperatures, and reduce thermal stress and thermal damage. At the same time, the thermal expansion coefficient of boron nitride crucible is low. In some high-temperature processes that require rapid heating or cooling, it can effectively reduce the occurrence of breakage or cracks and extend the service life.
In the field of semiconductor manufacturing, boron nitride crucibles are often used in high-temperature chemical evaporation, crystal growth and other high-temperature processing processes. Since boron nitride crucible can ensure the uniformity of its reaction and the quality of the final product, it is an indispensable crucible material in the semiconductor industry.
Other Ceramic Materials
In addition to the common ceramic materials mentioned above, there are also high-quality crucible materials such as magnesium oxide and beryllium oxide. They all have excellent high-temperature performance and are essential crucible container materials for many metal smelting and laboratories.
How To Ensure The Service Life of The Crucible?
If you want your crucible to have better performance and service life, you’d better do the following:
Storage:
It is best to store used crucibles in a dry, clean environment to prevent them from absorbing moisture and contamination. Storing crucibles near chemicals or in areas of high humidity should be avoided.
Operate:
You should use appropriate tools to operate the crucible, avoid direct contact with your hands, and check for cracks or damage after use.
Cleaning:
You should clean the crucible thoroughly after each use. All residues should be removed and care should be taken to allow it to cool properly before cleaning to prevent thermal shock and cracking.
FAQ
1. What is a crucible?
A crucible is a container designed for use at extremely high temperatures, primarily used for metal smelting and chemical reactions.
2. What is the melting point of a ceramic crucible?
The melting point of a ceramic crucible depends mainly on the material used. For example, an alumina crucible can withstand temperatures between 1650°C and 1700°C, while a zirconia crucible can withstand temperatures up to 2000°C.
3. What are the uses of ceramic crucibles in chemistry?
Ceramic crucibles are often used for high-temperature metal smelting, as chemical reaction containers, material processing containers, etc.
4. What is the function of ceramic crucible?
Ceramic crucible is mainly used for high temperature heating applications, melting or refining materials, etc. It can also act as a container for some chemical reactions.
5. What are the material properties of ceramic crucibles?
Ceramic materials have the characteristics of high melting point, low thermal expansion coefficient, good thermal stability, and chemical corrosion resistance.
6. Can ceramic crucibles be used to melt strong alkaline substances?
This mainly depends on the material of the crucible. Generally, we do not recommend that you use alumina crucibles to melt strong alkaline substances such as sodium hydroxide (NaOH) and sodium peroxide (Na₂O₂), as these substances may corrode the crucible.
7. What is the difference between porcelain crucible and ceramic crucible?
Porcelain crucible usually refers to a crucible made of porcelain material. Ceramic crucible has stronger performance than traditional porcelain crucible, can withstand higher temperature, and has stronger mechanical properties.
8. How to heat a ceramic crucible?
When heating a ceramic crucible, you should choose a suitable heating method according to the characteristics of the crucible material. It should be noted that sudden cooling or heating should be avoided during heating, which may cause the crucible to crack.
9. What are the maintenance methods for ceramic crucibles?
After using the crucible, you should clean it thoroughly to remove the residue, and use an appropriate cleaning solution to clean it, and finally rinse it with pure water and dry it for later use.
Conclusion
Ceramic crucibles are indispensable tools in modern chemistry and metallurgy. They are able to work in extreme temperatures and harsh chemical environments, playing a key role in a variety of scientific and industrial applications. Thank you for reading this article and hope it helps you.