O desgaste é uma ameaça persistente ao trabalho industrial, aumentando os custos, prolongando o tempo e comprometendo a eficácia geral das operações. Materiais cerâmicos são uma opção, reduzindo esses problemas. Carbeto de Silício (SiC) e Carbeto de Tungstênio (WC) são duas opções comumente disponíveis. Nós da Cerâmicas deslumbrantes, neste artigo compararemos os materiais e sua eficácia em aplicações de desgaste.
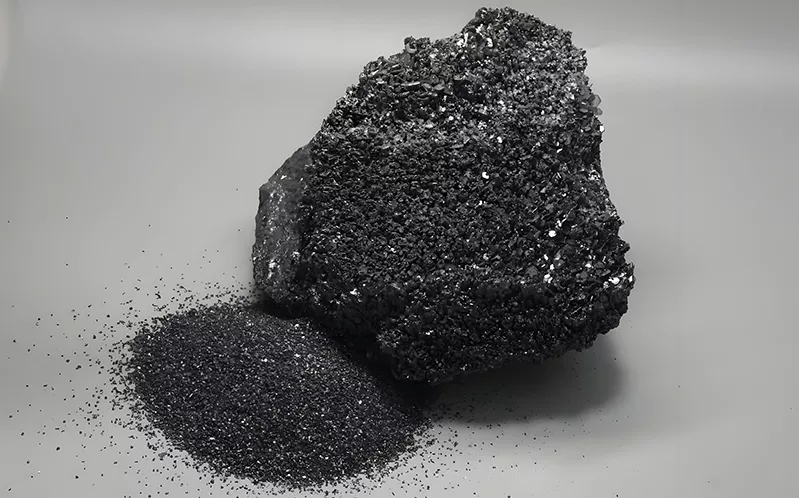
Carboneto de silício
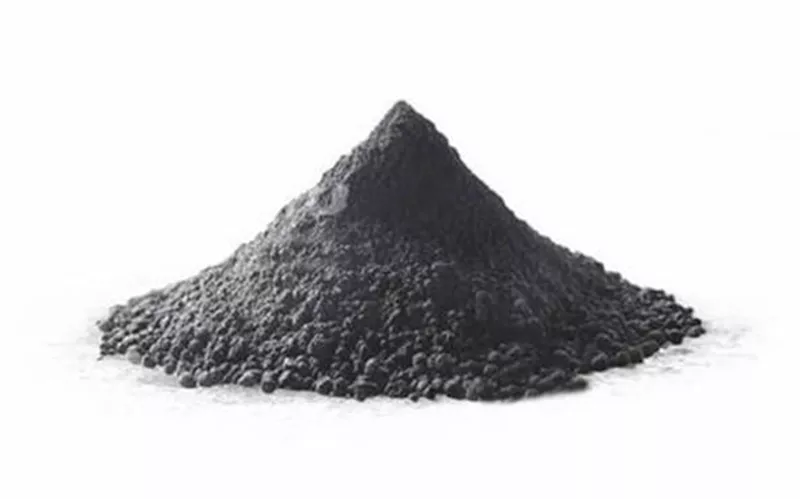
Carboneto de tungstênio
O que é carboneto de silício
O carboneto de silício é conhecido por sua adequação a aplicações químicas e sensíveis à temperatura. Este material é um amálgama de elementos de carbono e silício, cujos átomos formam ligações covalentes, conferindo ao material uma estrutura cristalina.
Depois do diamante, este é o elemento mais duro, o que o torna adequado para uma longa lista de aplicações que envolvem desgaste. Devido às propriedades não oxidáveis do carboneto de silício, ele é livre de corrosão, o que aumenta ainda mais sua confiabilidade.
O que é carboneto de tungstênio
Carboneto de tungstênio WC, como o próprio nome indica, é o produto de tungstênio e carbono fabricado por meio de um processo denominado SinterizaçãoO WC tem uma longa história de uso em aplicações industriais. Esses materiais são excelentes, seja em termos de resistência ao desgaste, abrasão, calor ou produtos químicos.
Carboneto de silício versus carboneto de tungstênio em aplicações de desgaste
O custo é um fator vital, mas não o único, que impacta a escolha do material de desgaste. A longo prazo, compreender a confiabilidade de um material em diferentes situações de trabalho, como pressão extrema, temperatura, abrasão e exposição a produtos químicos, é fundamental para compreender sua eficiência geral.
Carbonetos de tungstênio, por exemplo, têm preços elevados, o que se justifica por sua alta resistência à compressão de até 6833 Mpa. No entanto, em operações que envolvem temperaturas extremas, a deformação plástica torna grande parte dessa resistência inútil. Isso acaba tornando-os uma opção não muito adequada para aplicações de alta tensão. Por outro lado, materiais com resistência a altas temperaturas podem ser uma alternativa melhor.
Nesse contexto, o carboneto de silício (SiC) é uma opção a ser adotada. É mais frequentemente aplicado em operações que exigem alta resistência química e a altas temperaturas. No entanto, ambas as cerâmicas exigem uma análise cuidadosa de uma série de fatores na escolha. Esses fatores são discutidos a seguir.
Condições Abrasivas
A dureza da cerâmica é um aspecto primordial das aplicações de desgaste. Quanto mais dura a cerâmica, menor a probabilidade de danos. Na escala de Mohs, o nível de dureza do carboneto de silício é 9,5, superando o do tungstênio, que varia de 8,5 a 9. Portanto, o carboneto de silício é mais recomendado em aplicações sensíveis a abrasivos.
Em termos de densidade, o SiC está na extremidade inferior, com 3,21 g/cm³, muito abaixo dos 15,6 g/cm³ do Tungesten. Essa baixa densidade torna o carboneto de silício fácil de manusear. Além disso, sua alta resistência a arranhões o torna uma opção vantajosa para ambas as partes.
Lama pesada e condições extremas de bombeamento
Máquinas de polpa e bombeamento devem ser compatíveis para operar com eficácia em ambientes abrasivos e corrosivos. O carboneto de silício é considerado o melhor para trabalhar nessas condições. Seu baixo coeficiente de atrito garante desgaste e perda de energia mínimos.
Por outro lado, o carboneto de tungstênio, devido à sua ligação com cobalto, é altamente vulnerável a ácidos fortes. No entanto, isso pode ser controlado com revestimentos extras de cromo e molibdênio, mas isso resultará em altos custos finais. Portanto, o carboneto de silício é a escolha preferencial para tais aplicações.
Ambientes de alta pressão
Aplicações de perfuração, como petróleo e gás, envolvem altas pressões, e suas respectivas vedações devem ser fortes o suficiente para suportar essas pressões. Os carbonetos de tungstênio possuem uma boa combinação de alta densidade e resistência, sendo a escolha perfeita para esses casos. No entanto, se considerarmos apenas a resistência, os carbonetos de silício também são úteis, mas superados pelo tungstênio devido à sua alta densidade.
Mudanças rápidas de temperatura
Máquinas utilizadas em aplicações de alta temperatura, como fornos, devem ser fabricadas com materiais resistentes à temperatura. Portanto, a resiliência à temperatura deve ser levada em consideração ao escolher entre silício e carboneto de tungstênio.
O coeficiente de expansão térmica do carboneto de silício é de cerca de 4 a 4,5 × 10⁻⁶/°C, enquanto o do tungstênio é de 5,00 a 6,00 10⁻⁶/°C, o que é baixo e considerado o mais adequado. Mas isso não é tudo. Em relação à condutividade térmica, o silício também se destaca nesse parâmetro, com condutividade variando entre 120 e 170 W/mK, enquanto o do tungstênio varia de 84 a 100 W/mK.
Diferenças em durabilidade e resistência ao desgaste
O carboneto de silício se destaca em resistência mecânica e térmica. Em aplicações com alta probabilidade de desgaste e atrito, o SiC pode ser uma escolha confiável. Sua natureza não óxido, aliada ao seu baixo coeficiente de temperatura, previne a deformação e garante sua durabilidade em uma ampla gama de aplicações.
Por outro lado, a rigidez e a resistência do tungstênio são incomparáveis. Isso torna a cerâmica durável em aplicações de alta pressão por longos períodos. Portanto, para aplicações não vulneráveis à temperatura e à exposição a produtos químicos, o carboneto de tungstênio pode ser uma solução ideal.
Como escolher entre selos mecânicos de carboneto de silício e carboneto de tungstênio
Ao escolher entre silício ou carboneto de tungstênio, é importante entender primeiro a sua aplicação. Isso inclui considerar cuidadosamente diversos aspectos, como a presença de fluidos, faixas de temperatura, variações nos níveis de pressão, abrasão e probabilidade de corrosão.
A alta densidade do tungstênio, combinada com sua resistência mecânica, o torna amplamente compatível em aplicações de alta pressão. Em contrapartida, o carboneto de silício fica atrás apenas em densidade e apresenta maior resistência à corrosão, à temperatura ambiente e à abrasão. Os carbonetos de silício também permanecem bastante estáveis quando expostos a outros produtos químicos.
Com base na análise acima, é seguro afirmar que os carbonetos de silício são adequados para todos os tipos de aplicações de desgaste, exceto aquelas que envolvem pressão extrema. Além disso, seu preço, que é baixo em comparação com o tungstênio, o torna mais vantajoso, mas a escolha final depende das preferências de cada processo.
O resultado final
Tanto o carboneto de silício quanto o carboneto de tungstênio oferecem vantagens e limitações únicas. Embora o carboneto de tungstênio continue sendo uma escolha popular para aplicações industriais, o carboneto de silício surge como uma alternativa econômica e versátil. Cerâmicas deslumbrantes dedica-se a fornecer soluções inovadoras adaptadas às suas necessidades. Entre em contato conosco hoje mesmo para discutir seu projeto e descobrir como nossa expertise pode aprimorar seus processos.